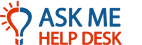 |
|
|
 |
Junior Member
|
|
Apr 8, 2009, 05:32 PM
|
|
Activity based cost
How can we find the activity based cost?
|
|
 |
Uber Member
|
|
Apr 8, 2009, 07:04 PM
|
|
Pretty broad question.
ABC costing is based on the idea that different types of activities will drive the costs of overhead, rather than just one main activity.
You have to take the costs for that activity, divide by the total amount of the activity (to get a rate to use), then multiply that rate by the activity level for each department or job or whatever you're doing.
A simple example just using two activities and two departments:
$100,000 cost for setups
$50,000 machine production costs
500 total setups
10,000 total machine hours
$100,000/500 = $200 per each setup
$50,000/10,000 = $5 per each machine hour
The above two are the rates, done basically the same way it would be done if doing "normal" overhead costing: estimated costs divided by activity.
You then apply it to departments using those rates, based on their activity. If Dept. 1 has 200 setups and Dept. 2 has 300 setups (500 total), then:
$200 rate x 200 setups = $40,000 for Dept. 1
$200 rate x 300 setups = $60,000 for Dept. 2
You would apply the machine costs in the same way, based on how many machine hours each department actually had.
Problems can be much longer than this, with more activities and more departments, but it's all still done the same way
|
|
 |
Junior Member
|
|
Apr 8, 2009, 10:22 PM
|
|
I tried to do this problem in the same way you told me, but got wrong answer.I need to explain this problem to somebody, So please help me to do this. I will be very thankful to you.Totaly :confused:
Provo Company produces two types of glass shelving, rounded edge and squared edge, on the same production line. For the current period, the company reports the following data:
Direct materials
Rounded Edge
$9,300
Squared Edge
$21,800
Total
$31,100
Direct labor
Rounded Edge
6,100
Squared Edge
12,000
18,100
Overhead (300% of direct labor cost)
Rounded Edge
18,300
Squared Edge
36,000
Total
54,300
Total cost
$33,700
$69,800
$54,300
Total
$103,500
Quantity produced
Rounded Edge
33,700/10,400ft.
Average cost per ft
$3.24
Squared Edge
69,800/14,100ft.
Average cost per ft
$4.95
Provo's controller wishes to apply activity-based costing (ABC) to allocate the $54,300 of overhead costs incurred by the two product lines to see whether cost per foot would change markedly from that reported above. She has collected the following information:
Overhead Cost Category (Activity Cost Pool)
Cost
Supervision
$
2,172
Depreciation of machinery
29,000
Assembly line preparation
23,128
Total overhead
$
54,300
--------------------------------------------------------------------------------
She has also collected the following information about the cost drivers for each category (cost pool) and the amount of each driver used by the two product lines:
Usage
Overhead Cost Category (Activity Cost Pool)
Total
Supervision
Driver Direct labor cost ($)
Rounded Edge
$6,100
Squared Edge
$12,000
Total
$18,100
Depreciation of machinery
DriverMachine hours
Rounded Edge
200 hours
Squared Edge
600 hours
Total
800 hours
Assembly line preparation
Driver Setups (number)
Rounded Edge
32 times
Squared Edge
95 times
Total
127 times
Assign these three overhead cost pools to each of the two products using ABC.
Product
Assigned Cost of
Rounded Edge glass
Squared Edge glass
 Originally Posted by morgaine300
Pretty broad question.
ABC costing is based on the idea that different types of activities will drive the costs of overhead, rather than just one main activity.
You have to take the costs for that activity, divide by the total amount of the activity (to get a rate to use), then multiply that rate by the activity level for each department or job or whatever you're doing.
A simple example just using two activities and two departments:
$100,000 cost for setups
$50,000 machine production costs
500 total setups
10,000 total machine hours
$100,000/500 = $200 per each setup
$50,000/10,000 = $5 per each machine hour
The above two are the rates, done basically the same way it would be done if doing "normal" overhead costing: estimated costs divided by activity.
You then apply it to departments using those rates, based on their activity. If Dept. 1 has 200 setups and Dept. 2 has 300 setups (500 total), then:
$200 rate x 200 setups = $40,000 for Dept. 1
$200 rate x 300 setups = $60,000 for Dept. 2
You would apply the machine costs in the same way, based on how many machine hours each department actually had.
Problems can be much longer than this, with more activities and more departments, but it's all still done the same way
|
|
 |
Uber Member
|
|
Apr 8, 2009, 11:05 PM
|
|
The problem has given you total cost for each type of overhead, and total activity base (driver), and you should be able to do it exactly like my example. (Excepts there's 3 instead of 2 different costs.) Therefore, I don't know what else to show you other than just doing your problem for you.
If you can show me your work that you discovered was incorrect, I could tell you where you went wrong -- without actually doing the work for you. That not only shows me where you're getting off, but you'll learn more from it that way.
One thing I can think of, though -- the instructions are saying to assign the overhead costs, but ultimately is it wanting total costs that include direct material and direct labor? Those costs still exist too.
|
|
 |
Junior Member
|
|
Apr 9, 2009, 03:52 PM
|
|
I figured out this problem. I was making mistake in supervision section. Well Thanks for you help
 Originally Posted by morgaine300
The problem has given you total cost for each type of overhead, and total activity base (driver), and you should be able to do it exactly like my example. (Excepts there's 3 instead of 2 different costs.) Therefore, I don't know what else to show you other than just doing your problem for you.
If you can show me your work that you discovered was incorrect, I could tell you where you went wrong -- without actually doing the work for you. That not only shows me where you're getting off, but you'll learn more from it that way.
One thing I can think of, though -- the instructions are saying to assign the overhead costs, but ultimately is it wanting total costs that include direct material and direct labor? Those costs still exist too.
|
|
 |
Uber Member
|
|
Apr 9, 2009, 04:53 PM
|
|
You're welcome. Glad you got it figured out!
|
|
Question Tools |
Search this Question |
|
|
Add your answer here.
Check out some similar questions!
Activity Based Costing in Accounting - Activity Drivers
[ 1 Answers ]
Hi,
I'm required to introduce Activity Based Costing in Finance branch of a Government Department. Does anyone know what Activity Drivers can be used for non-transactional based activities, such as preparation of Budgets, Annual Report, or other Accounting "common activities".
The way system...
View more questions
Search
|