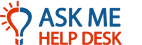 |
|
|
 |
New Member
|
|
Apr 25, 2007, 12:31 PM
|
|
Simple costing and ABC
Baker's delight (BD) has been in the food processing business three years. For its first two years (2005 and 2006), its sole product was raisin cake. All cakes were manufactured and packaged in one-pound boxes. BD used a normal costing system. The two direct-cost categories were direct materials and direct manufacturing labor. The sole indirect manufacturing cost category-manufacturing overhead-was allocated to products using pounds of production as the allocation base.
In its third year (2007), BD added a second product-layered carrot cake-which was also packaged in one-pound boxes. This product differs from raisin cake in several ways:
-more expensive ingredients are used
-more direct manufacturing labor time is required
-more-complex manufacturing processing is required.
In 2007, BD continued to use its simple costing system, in which it allocated manufacturing overhead using total pound (boxes) produced of raisin and layered carrot cakes. Direct material cost in 2007 was $0.60 per pound of raisin cake and $0.90 per pound of layered carrot cake. Direct manufacturing labor cost in 2007 was $0.14 per pound of raisin cake and $0.20 per pound of layered carrot cake. During 2007, BD sales staff reported greater-than-expected sales of layered carrot cake and less-than-expected sales of raisin cake. The budgeted and actual sales volume for 2007:
Budgeted actual
Raisin cake 160,000 lbs 120,000 lbs
Layered carrot cake 40,000 lbs 80,000 lbs
The budgeted manufacturing overhead for 2007 is $210,800
At the end of 2007, Jonathan Davis, the controller of BD, decided to investigate how an activity based costing system would have affected the product-cost numbers. After consultation with operating personnel, the single manufacturing overhead cost pool was subdivided into five activity areas. These activity areas, the cost-allocated base, the budgeted 2007 cost-allocation rate, and the quantity of the cost-allocation base used by the raisin and layered carrot cakes are as follows:
Activity Cost-allocation budgeted 2007 quantity of cost-allocation base
Base CPU of cost
Allocation base raisin cake layered carrot cake
Mixing labor-hours $.04 600,000 640,000
Cooking Oven-hours $.14 240,000 240,000
Cooling cool room-hours $.02 360,000 400,000
Creaming/icing machine hours $.25 0 240,000
Packaging machine hours $.08 360,000 560,000
Questions
1. Compute the 2007 product cost per pound of raisin cake and layered carrot cake produced using the simple costing system used in the 2005 to 2007 period?
Do I use the bugeted predetermine overhead rate? I am not understanding this.
2. Compute the 2007 product cost per pound of raisin cake and layered carrot cake produced using the activity-based costing system?
Do I need to allocated each volume with the cost per unit?
|
|
 |
New Member
|
|
May 19, 2008, 09:29 AM
|
|
Fgfgs
Fgrdf
|
|
 |
New Member
|
|
May 19, 2008, 10:31 AM
|
|
 Originally Posted by lcheng
Baker's delight (BD) has been in the food processing business three years. For its first two years (2005 and 2006), its sole product was raisin cake. All cakes were manufactured and packaged in one-pound boxes. BD used a normal costing system. The two direct-cost categories were direct materials and direct manufacturing labor. The sole indirect manufacturing cost category-manufacturing overhead-was allocated to products using pounds of production as the allocation base.
In its third year (2007), BD added a second product-layered carrot cake-which was also packaged in one-pound boxes. This product differs from raisin cake in several ways:
-more expensive ingredients are used
-more direct manufacturing labor time is required
-more-complex manufacturing processing is required.
In 2007, BD continued to use its simple costing system, in which it allocated manufacturing overhead using total pound (boxes) produced of raisin and layered carrot cakes. Direct material cost in 2007 was $0.60 per pound of raisin cake and $0.90 per pound of layered carrot cake. Direct manufacturing labor cost in 2007 was $0.14 per pound of raisin cake and $0.20 per pound of layered carrot cake. During 2007, BD sales staff reported greater-than-expected sales of layered carrot cake and less-than-expected sales of raisin cake. The budgeted and actual sales volume for 2007:
Budgeted actual
Raisin cake 160,000 lbs 120,000 lbs
Layered carrot cake 40,000 lbs 80,000 lbs
The budgeted manufacturing overhead for 2007 is $210,800
At the end of 2007, Jonathan Davis, the controller of BD, decided to investigate how an activity based costing system would have affected the product-cost numbers. After consultation with operating personnel, the single manufacturing overhead cost pool was subdivided into five activity areas. These activity areas, the cost-allocated base, the budgeted 2007 cost-allocation rate, and the quantity of the cost-allocation base used by the raisin and layered carrot cakes are as follows:
Activity Cost-allocation budgeted 2007 quantity of cost-allocation base
Base CPU of cost
Allocation base raisin cake layered carrot cake
Mixing labor-hours $.04 600,000 640,000
Cooking Oven-hours $.14 240,000 240,000
Cooling cool room-hours $.02 360,000 400,000
Creaming/icing machine hours $.25 0 240,000
Packaging machine hours $.08 360,000 560,000
Questions
1. Compute the 2007 product cost per pound of raisin cake and layered carrot cake produced using the simple costing system used in the 2005 to 2007 period?
do I use the bugeted predetermine overhead rate? I am not understanding this.
2. Compute the 2007 product cost per pound of raisin cake and layered carrot cake produced using the activity-based costing system?
Do I need to allocated each volume with the cost per unit?
Can you help me answer 1 and 2, thanks.
|
|
 |
Uber Member
|
|
May 22, 2008, 09:06 PM
|
|
Activity Cost-allocation budgeted 2007 quantity of cost-allocation base
Base CPU of cost
Allocation base raisin cake layered carrot cake
Mixing labor-hours $.04 600,000 640,000
Cooking Oven-hours $.14 240,000 240,000
Cooling cool room-hours $.02 360,000 400,000
Creaming/icing machine hours $.25 0 240,000
Packaging machine hours $.08 360,000 560,000
Questions
1. Compute the 2007 product cost per pound of raisin cake and layered carrot cake produced using the simple costing system used in the 2005 to 2007 period?
Do I use the bugeted predetermine overhead rate? I am not understanding this.
You're to use the above given information. First, ignore most of the jibberish. It's just making things complicated and activity based costing just isn't difficult. It's no different than buying 5 gallons of milk for $3.50 each and wanting to know the total you spent. Except that you also bought chocolate milk at a different price, and orange juice at yet another price. So you have a price per item, and how many you bought, so you can figure out how much you spent on each item separately. And then you can total it all to see how much you spent in total.
That's really all you're doing. The difference of a normal costing basis is the assumption that the same activity is causing the costs with each different item, jump lumping it altogether, and charging by the same rate. ABC costing is taking into consideration that each product could be more heavy in one activity than another, that one product may be more machine-based and one more labor-based, etc. So instead of lumping, it divides up all the different types of overhead costs into categories, and charges them separately for each product.
Your overhead is consisting of five different activities. They add up to .53 total. But you're not going to charge .53 per (per what? - they're all based on different things.) Rather, you charge each of the 5 activities separately. i.e. 4c per mixing labor hour. Mixing is labor intensive, so "labor" is the activity they are using to apply overhead. So you apply it at 4c per labor hour. And on down the line. So you have 5 separate activities to do, for 2 different products. The total of the 5 is the total overhead.
2. Compute the 2007 product cost per pound of raisin cake and layered carrot cake produced using the activity-based costing system?
Do I need to allocated each volume with the cost per unit?
I'm not sure what your question means. But the above calculations will give you the overhead, and the problem has given you the two direct costs, material and labor, and the amount that were sold. Direct costs are charged directly to the product, just like the price of a gallon of milk. Total costs include the material, labor and overhead.
|
|
 |
New Member
|
|
Nov 13, 2008, 10:39 PM
|
|
 Originally Posted by lcheng
baker’s delight (bd) has been in the food processing business three years. For its first two years (2005 and 2006), its sole product was raisin cake. All cakes were manufactured and packaged in one-pound boxes. Bd used a normal costing system. The two direct-cost categories were direct materials and direct manufacturing labor. The sole indirect manufacturing cost category-manufacturing overhead-was allocated to products using pounds of production as the allocation base.
In its third year (2007), bd added a second product-layered carrot cake-which was also packaged in one-pound boxes. This product differs from raisin cake in several ways:
-more expensive ingredients are used
-more direct manufacturing labor time is required
-more-complex manufacturing processing is required.
In 2007, bd continued to use its simple costing system, in which it allocated manufacturing overhead using total pound (boxes) produced of raisin and layered carrot cakes. Direct material cost in 2007 was $0.60 per pound of raisin cake and $0.90 per pound of layered carrot cake. Direct manufacturing labor cost in 2007 was $0.14 per pound of raisin cake and $0.20 per pound of layered carrot cake. During 2007, bd sales staff reported greater-than-expected sales of layered carrot cake and less-than-expected sales of raisin cake. The budgeted and actual sales volume for 2007:
Budgeted actual
raisin cake 160,000 lbs 120,000 lbs
layered carrot cake 40,000 lbs 80,000 lbs
the budgeted manufacturing overhead for 2007 is $210,800
at the end of 2007, jonathan davis, the controller of bd, decided to investigate how an activity based costing system would have affected the product-cost numbers. After consultation with operating personnel, the single manufacturing overhead cost pool was subdivided into five activity areas. These activity areas, the cost-allocated base, the budgeted 2007 cost-allocation rate, and the quantity of the cost-allocation base used by the raisin and layered carrot cakes are as follows:
Activity cost-allocation budgeted 2007 quantity of cost-allocation base
base cpu of cost
allocation base raisin cake layered carrot cake
mixing labor-hours $.04 600,000 640,000
cooking oven-hours $.14 240,000 240,000
cooling cool room-hours $.02 360,000 400,000
creaming/icing machine hours $.25 0 240,000
packaging machine hours $.08 360,000 560,000
questions
1. Compute the 2007 product cost per pound of raisin cake and layered carrot cake produced using the simple costing system used in the 2005 to 2007 period?
Do i use the bugeted predetermine overhead rate? I am not understanding this.
2. Compute the 2007 product cost per pound of raisin cake and layered carrot cake produced using the activity-based costing system?
Do i need to allocated each volume with the cost per unit?
1) raisen cake 2335
Layered carrot cake 456
|
|
Question Tools |
Search this Question |
|
|
Add your answer here.
Check out some similar questions!
Job Costing versus ABC costing system
[ 0 Answers ]
Question
A machine facility specializing in jobs for the aircraft-components market previous simple job-costing system had two direct-cost categories (direct materials and direct manufacturing labour-hours). The indirect cost-allocation rate of the simple system for 2007 would have been $115...
Absorption costing profit from Marginal costing profit
[ 0 Answers ]
I know my opening stock and closing stock figures and I have worked out my annual profit using marginal costing. I also know my fixed overhead absorption rate.
Using these figures, what formula do I use to calculate my profit using absorption costing?
Need abc help to format hard drive
[ 15 Answers ]
My PC will not start windows.
I have had my PC checked and the verdict is format the hard drive.
My ops is windows xp
Any advice to get me started would be appreciated
View more questions
Search
|