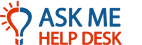 |
|
|
 |
Full Member
|
|
Feb 21, 2009, 11:37 PM
|
|
Framing a flat roof
I am getting ready to embark on a home addition. It will be 10'x5' and will be three stories high. The rest of my home has a flat roof and for consistency sake we would like the addition to have a flat roof as well. Can anyone help me figure out how to frame a flat roof?
The addition will be tying into a brick house, so on one side the rafters will be attached to a ledger board, on the other side they will rest on a double sill plate created by a new wood framed exterior wall.
First, given the addition is small, what size rafters do you suggest, will 2x10s suffice? What about 2x12?
Second, what sort of slope is necessary for a flat roof?
Finally, how do you frame it to get that slope?
|
|
 |
Ultra Member
|
|
Feb 22, 2009, 09:22 PM
|
|
Hi Stubits. This has to be the smallest 3 story addition I have heard of in 30+ years of building.
So to answer the floor joist size. This will depend somewhat on the size of the floor joist you have on the main structure so the door to each floor works in elevation. Unless you don't care to maintain the same ceilings heights the main house has.
A 2x8 16 o.c. at 5 feet is good if the code allows it
As far as the Roof pitch, a 1/4 per foot min is what I go by for "flat" roof. I also you 0.60 rubber for for the flat.
Now here's what you may want to think about for the roof. How much insulation thickness you need and it needs to vented.
You ask how to bulid the flat roof. This depends on the adjoining roof beside it, and which way it slopes. You could continue the same slope being the add is only 5 feet wide. You could knee wall it above the other flat roof and pitch it either way. With knowing the specifics of the old off heights or slope I'm just giving ideas here.
Signed 21 Boat
If I Helped To Answer Your Question Please Rate My Answer
|
|
 |
Full Member
|
|
Feb 23, 2009, 08:26 AM
|
|
21 Boat-
This is great info! I'd rate your answer, but the system wants to me rate someone else first.
It is a small addition, but just right for us, really. It will help us gain an extra 1.5 baths, which is all we really need.
As for the floor joists, we are actually planning on using 2x12s throughout, mostly because there will be lots of plumbing, and as such, unfortunately some holes will need to be drilled in the joists, not too many, but a couple, for sure. We aren't too concerned with maintaining ceiling heights, as our ceilings are rather high, but we are working to make sure to keep the doors at the same elevation. Thanks for all your advice on those points.
As for the roof itself, we are looking for R-36 level insulation. Our current roof isn't vented (it's a 75 year old home). How are flat roofs typically vented? Please see the accompanying photo, we are effectively enclosing the dog ear area of the home's footprint. I guess what I am trying to figure out is specifically how to frame the flat roof. We'll install ledger boards along the long brick wall for the floor joists and I am thinking I will do the same for the roof, right? Given that the roof will slope down over 10', the base of the roof will be approximately 2.5" lower than the top, right? I think I understand how to do that on the ledger board, but how does that work on the other side, where the joists rest on the stick framed wall? Do I notch the joists slightly as they go down?
I've never built a roof before, let alone a flat one, so any help would be much appreciated! I will hire a rougher to actually finish the roof off, but I plan on framing it myself. The roofer will flash it, etc.
Thanks!
|
|
 |
Ultra Member
|
|
Feb 23, 2009, 12:28 PM
|
|
After I posted I thought about possible mechanicals in the floor joist.
As far as venting the flat roof, here's s a site that has vents for intake and exhaust. One vent pushes air in and the other takes it out.
Rooftop System
Framing the roof should be 2x12s. The reason is you need the rafter depth at the end where the rafter sits on the outside wall to be high enough off the house plate to get "R" value and a 2" air space "baffels" above that.
Since your home is 75 years old and if its all brick you could use the brick wall and cut rafter pockets in the brick since all double brick walls are considered a bearing wall. Again just giving possibilities here.
I would cut a seat for the rafter to go on new double plate. Also I would use Simpson HZ.5AZ hurricane straps.
Builders Hardware - Building Materials at The Home Depot for the rafter to the top plate on both sides.
Check your codes.
Are you going to have any kind of overhang on the new roof?
Signed 21 Boat
If I Helped To Answer Your Question Please Rate My Answer
|
|
 |
Full Member
|
|
Feb 23, 2009, 12:41 PM
|
|
21-
This is excellent information. Many, many thanks.
I've considered the idea of cutting rafter pockets right into the brick, but in the end I think using ledger boards will be easier for me to do, and I believe I'll end up with the same strength, etc. I'd do this for both the floor joists as well as the roof. This should work OK, right? I'd be bolting the ledger board to the brick wall.
So, a couple of quick questions. First, for the upper level of the addition, are the ceiling joists and the roof joists the same? Or do I install ceiling joists and then install a separate set of roof joists above that?
As for the roof construction, I am still confused (sorry!). I am attaching a photo that might help. You see the cutback in the house, right? That's where the addition will be. So, the right wall will be the brick wall, where I will install the ledger boards, and the back wall will be the brick wall. The right wall will actually be built on top of the basement to the left (which is actually a party wall on my property (the city and the neighbor have agreed). What I am just not understanding is how to handle the roof joists where they rest on the stick framed wall on the left. What do you mean by "cut a seat" for the rafter to go on?
Thanks! Sorry I am just not able to picture it!
|
|
 |
Ultra Member
|
|
Feb 23, 2009, 01:27 PM
|
|
 Originally Posted by ;
Or do I install ceiling joists and then install a separate set of roof joists above that?
It a matter of looking at a flat ceiling inside or a slanted ceiling. Either or can work.
18. Laying Off Common Rafter Seat Cut And End Cut
Measuring, Marking & Layout: A ... - Google Book Search
This should help you. The seat is cut in the rafter and makes a bird mouth.
So far I don't see any pictures ? Check your post.
Signed 21 Boat
If I Helped To Answer Your Question Please Rate My Answer
|
|
 |
Full Member
|
|
Feb 23, 2009, 01:31 PM
|
|
Here is the pic, sorry!
|
|
 |
Ultra Member
|
|
Feb 23, 2009, 05:29 PM
|
|
Good image. I assume you are going to slant the roof from the back of the alcove towards the front coming towards me.
You have what is called a parapet wall in the alcove that protects the rain from coming down on the steps. Use the brick for a ledger/nailer to attach adjustable rafter hangers. When you or whoever puts the rubber roof on use a side drip edge that has a standing seam. This will act as a parapet wall and control the water from running over the side edge dumping rain on the neighbors
A standing seam drip edge is what's used for a built up roof or a tar roof. Its like a regular drip edge but it a has a little 90 dergee at its edge that is flat if its standard drip edge.
Signed 21 Boat
If I Helped To Answer Your Question Please Rate My Answer
|
|
 |
Full Member
|
|
Feb 23, 2009, 06:46 PM
|
|
I'll definitely hire a pro to do the roof. Can't imagine a 10'x5' roof is going to be all that expensive and it pays to have it done right. That said, thanks so much for the heads up on the standing seam drip edge... I will be sure to remember that.
Would something like this work as an adjustable hanger? THA/THAC/THAR/L Adjustable Truss Hangers
So, it seems as though you have lots of experience with this stuff. Would you mind if I asked you a couple of additional questions?
1) The addition will be constructed with wood studs, of course, and covered in Hardie Panel (Hardie's vertical siding. My question is, how do I handle the vertical seam between the addition, Hardie panel, and the original home, brick. Clearly I cannot just but the Hardie Panel up to the brick as water could easily enter, but would flashing work in the application?
2) So, a bit of a math question. Is it possible and code friendly to run 3" PVC through 2x12 joists for a distance of 13' while keeping the 1/4" per 1' slope? I guess I will have to go through about 12 joists. Like I said, the joists are 2x12s and span about 16'. They are 16" OC. I have done the math and I think the answer is yes, but would appreciate any insight.
Thanks!
|
|
 |
Ultra Member
|
|
Feb 23, 2009, 07:42 PM
|
|
This is the styles of hangers I was referring too.
Simpson Strong-Tie Video Library
Yes use flashing in the corner where the brick and new wall meet.
Where did the 16' joist come from? I thought the add was 10'
I not sure what your insp is there but I wouldn't be running a 3" through 13 feet of joist. Can the joist be turned if these are new joist?
Check with the inspector. He may say no, or make you sister up where the joist are going to be hole sawed for the main sewer line. Can you drop that sewer line in a built corner chase-way? Or run a soffit under the joist?
Signed 21 Boat
If I Helped To Answer Your Question Please Rate My Answer
|
|
 |
Full Member
|
|
Feb 23, 2009, 08:49 PM
|
|
Once again, thanks!
Those hangers make sense. Simpson has so many options!
16' joists exist in the current house. The joists for the addition will be just 5' spans. Since they are existing joists, turning them just isn't an option, and frankly, neither is sistering given the space is finished. A soffit would work, for sure, but I was hoping to avoid it. I will check with the inspector to get his opinion. Generally though, you'd advise against it, right?
Ok, so, for flashing between the addition and the current wall. I was planning on caulking the joint well. Some people have suggested I set the finished addition wall back a little from the brick wall, what do you think about that? What sort of flashing would you recommend using? I cannot come up with anything that seems like it would help?
|
|
 |
Ultra Member
|
|
Feb 24, 2009, 06:06 PM
|
|
I wouldn't worry about the brick corner for sealing.
When you go to sheet in the side and I assume you are going to use OSB ext sheeting. Just use 100% silicone caulk the edge of first sheet as you butt that against the brick. After the OSB and what ever house wrap you use. Install the corner flashing with the one end bent at a 90 to the with of the siding " hardie plank" this will double seal at the initial façade and the back up is the sheeting is also sealed.
Setting the wall back really doesn't do anything. If water gets to the OSB its going be a problem weather its slipped back behind the old brick return wall or not.
Signed 21 Boat
If I Helped To Answer Your Question Please Rate My Answer
|
|
 |
Full Member
|
|
Feb 25, 2009, 09:59 AM
|
|
21 Boat-
Thanks so much. Just yesterday I found a great guide by Hardie. Here is an image of what they suggest. If I follow this, I should be fine, right? Or would you suggest anything further?
Also, it is a multistory house and so the instructions indicate I need to run horizontal Z-flashing at each floor division. How to I handle where the horizontal z flashing meets the corner flashing?
Moving even further off topic(!), the house currently has forced air heat and AC. We'd like to have a vent in each of the three floors (just one as each floor is only 50 sq. ft), but the ductwork for the first two floors would have to run through those solid 8" thick brick walls. Any suggestions? Getting the ductwork to the wall isn't an issue, but getting it through is. Any thoughts?
|
|
 |
Ultra Member
|
|
Feb 25, 2009, 02:57 PM
|
|
Hi Stubits I never used Hardie siding here in Pa. But what I'm wondering is what is the 1x4/2x4 end for?
The basic here on the warning from hardie say never butt the siding against the brick which I agree 100%, Apparently they don't want the lap siding to get close to and end wall.
I looked up hardie and read it has a 50 year transferable warranty. What's strange there trim board is only 15 years warranty
This proprietary process for fiber cement trim ensures uniform coverage of sealer and primer, providing an excellent surface for paints. HardieTrim boards come with a 15-year transferable limited warranty.
This proprietary process ensures uniform coverage of sealer and primer, providing an excellent surface for paints and also resisting fungus and mildew. HardiePanel vertical siding comes with a 50-year transferable limited warranty.
I would follow hardies specks to the tee to maintain the warranty. The flashing between the floors is a good question. I would guess they want horizontal flashing every 8 acting as a weep moisture system. The siding must be prone to moisture behind it?. and needs to weep out every so often.
As far as the heat/AC. Its dusty to punch through the brick but We commonly due it as all other contractors. Hears the most important issue. Get at least 3 HVAC contractors to look at you system to make sure it can handle the added addition. Heat fairly easy but AC is a heavy air to push and move. Also think of air returns for each floor.
Example a 90 on a heat run is equivalent to the same resistance and push as a 10' straight pipe.
The horizontal flashing I assume comes with the hardie system. If it does then it mimics the lap siding and sheds water and what ever gets past that is still shedded in the counter flashing where brick meets new wall
Signed 21 Boat
If I Helped To Answer Your Question Please Rate My Answer
|
|
 |
Full Member
|
|
Feb 25, 2009, 06:17 PM
|
|
So, what do you use for siding up in PA? Do you have a favorite?
I think the trim is mostly decorative from what I've read and not really required.
The horizontal flashing makes sense to me, but do you have any thoughts on how to handle where it intersects with the vertical corner flashing?
The good and the bad news is that my HVAC system is WAY oversized. We bought the house about 6 months ago and the previous owners had installed a 5 ton air handler in our 1,400 sq. ft. home. We have more than enough capacity to add a couple of extra vents. I'll be sure to add return air vents in all but the bathrooms.
So, aside from all the dust, no worries cutting through the brick, structural I mean? Do I need to add lintels? Or just cut open a hole?
Thanks!
|
|
 |
Ultra Member
|
|
Feb 25, 2009, 07:17 PM
|
|
Hears the simple science when cutting through a brick or block wall and what needs supported directly above that cut out.
Weather its block or brick, you look at the opening you want and the top center of that opening. From each side follow the masonry joints heading towards the center of the opening like going up steps following the bed and head joints. When you reach the center of the opening you want, look at the wall size below you (a triangle( that wall area is what will need supported by a header/angle iron/flat steal.
This basic structural science applies perfectly until these variables change. There needs to be enough lateral side weight and volume where you start the steps to support the arch itself. Also if the opening is big and you get to the top and didn't reach the center of the stepped arch, then the load above that will be direct down pressure to your opening below.
I maybe got to deep on cutting openings in masonry, One job alone for me were 28 windows cut in a 4 story all brick ware house for reg windows. Been cutting through masonry structures for 30+ years. Being a mason as my first trade makes it easy for me.
It goes back to the natural arch support. Except your arch is in brick courses that are stepped.
On a small opening like duct work many times there are no lintel's put in for header support. Some times we will just put in some flat steel and grove out the side brick joints and that just carries the brick above.
The duct work you need for those small rooms will more than likely be 6" round or less. If flex duct are used then a metal "thimble" is used to to sleeve through wall.. They also may use 2 1/4 x12 wall stack to punch through and boot the end for grill.
I have no real favorite siding except brick or shadow rock. My town was founded in the 1700s and is all brick in the city. The newer houses have vinyl/ fake stone/ brick or stone. Stucco also
Signed 21 Boat
If I Helped To Answer Your Question Please Rate My Answer
|
|
 |
Full Member
|
|
Feb 25, 2009, 07:20 PM
|
|
Thanks so much. I am going to be doing as much of this myself as possible, so it is good to know my options. Which would you suggest, round duct or the wall stack?
|
|
 |
Ultra Member
|
|
Feb 25, 2009, 07:39 PM
|
|
Actually both can be applied. When you run a heat run with round pipe and then need to go up through a floor you use a "boot" that goes from round to 2 1/4x12 which can connect to a wall stack or a floor register can connect there.
A wall stack is commonly used when AC is involved. It fits between a 2x4 studded wall. The stack is in that wall cavity and two openings are cut into it for l closeable grills.
In the winter you shut the top grill and open the bottom so heat comes out the bottom. For A.C. you do the opposite. The AC comes out of the top grill (bottom closed) " wall stack" hi lo is the best way to control/distribute the warm and cold.
To many times I'm in a home and the top floor has a floor register which is fine for heat. But for AC it's a bust. The cold air lays on the floor, goes under the door bottom and drops down the steps. That's a perfect way to screw up AC.
Many times the air return is in the common floor hall and that helps suck out the low lying cold air right out of the bedrooms and down the steps
Signed 21 Boat
If I Helped To Answer Your Question Please Rate My Answer
|
|
 |
Full Member
|
|
Feb 26, 2009, 11:02 AM
|
|
Ok, so lots here.
First, I am not actually using the Hardie Plank siding, instead, the vertical Hardie Panel. The horizontal flashing isn't part of the system, just standard z-flashing. I guess my question is, when I get to where the horizontal (z-flashing) and the vertical (corner flashing) meet, how do I handle it? Do I run the z-flashing right on top of the corner flashing? Under? Do they butt up against one another?
On the HVAC, our system isn't too advanced. It isn't easy running HVAC in a 75 year old rowhouse with solid brick party walls. On the main floor of the house all the supply vents are on the floor. In the basement and the second level of the home they are on the ceiling. In the addition we are going to keep 2 of the 4 walls as exposed brick. It gives us a little extra clearance and we like the look a lot. Also, with the exception of the new upper level bath, the addition rooms will be connected to currently heated/air conditioned space without doors. I figure we'll maintain the current setup, vents in the floor on the main level and in the ceilings on the other two.
|
|
 |
Uber Member
|
|
Feb 26, 2009, 03:59 PM
|
|
One question I have for the OP
Since this is obviously a row home and this is the back door entrance for both homes... Have you asked your adjoining neighbor if they have any objections to this "addition" you intend on doing? I'd ask before starting the project.
|
|
Question Tools |
Search this Question |
|
|
Add your answer here.
Check out some similar questions!
Insulation of flat roof
[ 7 Answers ]
I just had the roof and plywood replaced over a 1950s addition. I exposed the rafters in the ceiling below. My question is, after I insulate with 6 1/2 kraft faced, what can I use for a vapor barrier, between insulation and sheetrock?
Tarping a flat roof
[ 2 Answers ]
Hello need some help trying to tarp a flat roof with a/c unit on it what is the best was to stop water from coming in around the units don't want to cover the a/c unit they will burn up
Attach gable roof to flat roof
[ 1 Answers ]
We are building a three season attached screenroom. We are uncertain how to attach the gable roof to the present roof (gabled in the opposite direction, so the attachment is on the flat side). We have spent hours trying to locate do it yourself instructions and can only find do it yourself kits...
Shingles not flat on new roof
[ 5 Answers ]
Just had a new roof installed with all new plywood etc. Looks like a fine job except that most of the shingles do not lie 100%flat on the bottom. Someone told me that it's because the weather is still cold (it was installed beginning of December in NY) and that if it were warm, that the shingles...
Roof framing
[ 1 Answers ]
How to lay out and cut roof rafters
View more questions
Search
|