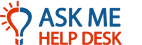 |
|
|
 |
Full Member
|
|
Mar 5, 2009, 06:08 AM
|
|
Ok, I totally get this now. Great explanation. So, as always, a couple of questions...
1) Why is this necessary? I don't doubt you at all, just want to understand why the "beam" is necessary as opposed to just a standard joist which would normally be sufficient.
2) How many joists should I "double up"?
3) Is it necessary to pocket it into the brick? Or can I just attach it to the ledger board like the rest of the joists?
|
|
 |
Ultra Member
|
|
Mar 5, 2009, 09:10 AM
|
|
You more less have an "L" shape wall you are adding. There isn't any ledger board on that opposite wall. Ledger on existing side and complete new wall opposite side. New joist go over that wall (10) side.
Because of a new brick veneer on the 5' front wall which address 4 1/2" to that front wall, plus 1/2" OSB behind new brick wall then Studs. The front and Side Wall is thicker than the second floor since you want to do new brick on first floor/ ground wall only and not the other floors..
The Joist/Beam is to help off set the beginning of the second floor and get far enough over the top of the stud plate and also the 4 1/2" brick wall to flush 2x12 joist to the outside of those " brick wall to flush 2x12 joist to the outside of those " shape wall.
On the 5' end wall you are going to need an added joist for a nailer for the ceiling below to hang drywall on the ceiling which can be added as part of the Joist beam.
Remember I suggested to offset ( going towards the house standing in yard looking at the back of the new addition as it were) the 5' part of foundation towards the house and back from the existing brick wall 3"+ for the new brick veneer to have a small inside corner where it Butts to old.
This will help and allow the Joist beam to be pocketed into the existing wall for load carry of the offset 2nd floor wall. The 3" shape wall.
On the 5' end wall you are going to need an added joist for a nailer for the ceiling below to hang drywall on the ceiling which can be added as part of the Joist beam.
Remember I suggested to offset ( going towards the house standing in yard looking at the back of the new addition as it were) the 5' part of foundation towards the house and back from the existing brick wall 3"
Now Just to throw you a big loop here is move the yard 5' end PAST the existing wall and now you have a brick return wall of '?" inches and A smaller Joist/beam in width will be needed
1) Why is this necessary? I don't doubt you at all, just want to understand why the "beam" is necessary as opposed to just a standard joist which would normally be sufficient. The beam is to carry the next two floor loads since its being offset to flush to first floor brick veneer. Part of the second floor load will be resting on the 1st floor brick veneer and since the joist beam is WIDE WALL ( brick veneer/ studs)
2) How many joists should I "double up"? Starting from the inside studs ( 1 1/2"+ old brick on existing will HIDE the new Joist/beam and protect it. This will also help break up the vertical mortar joint. And lastly it will be far enough back that when you slip the 2nd floor OSB over the new brick below and add the Hardie siding you will be at a finish reveal of around 1") brick veneer ( 4 1/2" )
3) Is it necessary to pocket it into the brick? Or can I just attach it to the ledger board like the rest of the joists? Hard to find hangers for a wide beam/joist not to mention a beam pocket into masonry is the best. Can't get better support than that.
Signed 21 Boat
If I Helped To Answer Your Question Please Rate My Answer
|
|
 |
Full Member
|
|
Mar 5, 2009, 09:21 AM
|
|
Wow, so like 7 or 8 joists all joined together?
|
|
 |
Ultra Member
|
|
Mar 5, 2009, 09:49 AM
|
|
Yep You can use Ply between to tweak the distance width. Kind of a partial micro lamb beam
And No you don't want to buy one of those here. Very expansive.
Signed 21 Boat
If I Helped To Answer Your Question Please Rate My Answer
|
|
 |
Full Member
|
|
Mar 5, 2009, 10:05 AM
|
|
Ok, this totally makes sense.
How much of an inside corner are we looking for with the offset? Are you suggesting setting the new 5' wall back 3" from the current wall?
|
|
 |
Ultra Member
|
|
Mar 5, 2009, 10:45 AM
|
|
Yes any further in and the offset from there will take more notch out of beam to address the vertical load shift.
Signed 21 Boat
If I Helped To Answer Your Question Please Rate My Answer
|
|
 |
Full Member
|
|
Mar 5, 2009, 01:29 PM
|
|
OK, great.
So, in this case, would the mason still attempt to work the new brick in with the old brick? Or will there just be an inside corner with a vertical seam?
|
|
 |
Ultra Member
|
|
Mar 5, 2009, 02:40 PM
|
|
I would use a good gaged brick walls ties every 8" and pop out the old brick wall every 16" inches or what works in that general spot for the brick courses. Reg brick usually works to the 6 or 7 on the brick spacing rule.
So just brake a out half brick on old wall and then use a full brick to lay in the pocket and the other half is in the new wall
The common ones are the corrugated ties. You can use a masonry nail to tie them in, but I like the short Tap Cons screws
TN 44B - WALL TIES FOR BRICK MASONRY
Signed 21 Boat
If I Helped To Answer Your Question Please Rate My Answer
|
|
 |
Full Member
|
|
Mar 9, 2009, 07:21 AM
|
|
Ok, so I have been thinking about this project all weekend long, running through a lot of different variables and I have a couple of questions and some changes to my original thinking... I hope you're still monitoring this!
First, I am thinking it might be easier for the HVAC, plumbing and electrical to run the floor joists so that they span the 10' distance rather than the 5' difference. Do you see any problems with that? I also believe that that will allow me to cantilever the 5' exterior wall out over the brick veneer, right?
Now, on the first level (where there is currently a concrete landing), would it be possible to run a 2x12 ledger board from the 10' brick wall across the 5' span to rest on the opposite wall. Then, I'd run the joists off the ledger board using Simpson joist hangers, cantilevering the floor joists over the 5' exterior wall by a few inches to match up the siding to the brick. Will that work?
Thanks!
|
|
 |
Ultra Member
|
|
Mar 9, 2009, 11:46 AM
|
|
That's what I mentioned a while back. This also Completely solves the cantilever bearing on the front 5' wall. I was going to post back because of the mechanicals having a problem using the joist bay for HVAC. The 5 ' way. not to mention wiring. Add to that less brackets and frame time. If that brick wing wall is sound then that can be added to and Incorporated into. Again check codes. At this point I see no problems.
Signed 21 Boat
If I Helped To Answer Your Question Please Rate My Answer
|
|
 |
Full Member
|
|
Mar 9, 2009, 12:04 PM
|
|
Thanks for your patience with me, sorry I didn't listen better earlier. I will definitely go with the above approach.
OK, some more questions on the footings/foundation. So far as I can tell, there are really three parts to this. One is the poured footer itself, the second is the block foundation wall and third is raising the height of the cement floor.
So, can I run through this with you again?
STEP 1
First I will excavate so that I can pour a footing according to code, but let's assume 20" wide by 8" deep for the full perimiter of the addition. I will tie it into the current footing using rebar on both sides and will reinforce the footing with additional rebar. Also, I will include vertical rebar to tie the footer into the foundation wall, right?
Step 2
I will build the foundation wall using 10" cmu's, switching over eventually to 6" cmu's to provide a brick ledge. I will have J Bolts at the top to tie in the framing.
Step 3
This is where I still have questions. What is the best way to build up the current concrete slab. I believe it is likely 4" thick already and we need to pour just 3" more to bring it up to the current floor. Do I do this after I've laid the foundation walls? Do I need to tie the new slab into the old slab or can one float over the other? Am I better off just breaking up the old stuff?
Thanks!
|
|
 |
Ultra Member
|
|
Mar 9, 2009, 03:06 PM
|
|
1. 20" wide by 8" deep...
Code for here is 3' deep to get below frost line. The footer should be min 24" wide so you can step in the ditch and lay the block. Footer 8" thick with bar as far as I'm concerned is perfect and over code here. ( Its three stories) so for me bar is a given. To tie into existing walls use bar horizontally from middle of new 8" footer to adjacent walls.
2. I will build the foundation wall using 10" cmu's, switching over eventually to 6" cmu's to provide a brick ledge. I will have J Bolts at the top to tie in the framing...........
Perfect. Just remember you need a 4"high/thick cap block 6" wide for house plate. Before you back fill the new block walls. You need to parge it from finish grade down or the whole wall. Then use foundation coating after parge is fey and coat from finish grade down to footer. Now you can backfill new wall.
3. Do I need to tie the new slab into the old slab or can one float over the other? Am I better off just breaking up the old stuff? ..........
Yes I would for these reasons. To do a good job os break up the concrete. From finish floor down would be. 4" new concrete. 6 mil ploy vapor barrier/ 4" crushed 2B clean stone. Now remember my previous post on insulating the perimeter of the concrete floor under the concrete
Signed 21 Boat
If I Helped To Answer Your Question Please Rate My Answer
|
|
 |
Full Member
|
|
Mar 9, 2009, 07:52 PM
|
|
Excellent.
Given the size of this job, do you think it is OK for me to do the foundation work myself? If I follow the directions you've given, I should be OK, right? Or do you think I should hire this out?
Ok, couple of follow-up questions. Is the timing right? First I will pour the footer, next build the block wall and then pour the slab? Is there anyway to pour the slab and the footer at the same time? This way I could avoid having the ready mix truck come out for two tiny loads.
If I chose to not break up the current slab (not sure yet what I want to do), would you recommend tying it into the new slab somehow or just float the new slab on top?
|
|
 |
Ultra Member
|
|
Mar 9, 2009, 09:05 PM
|
|
That's a tuff question. I don't know your skill level. Check with city on codes get permit.
Dig out the ditch. Prep footer with rebar. To figure out your concrete a Yd of Crete is 46.656 cubic inches. To a yard.
Hear comes the tradesmen lingo. When you lay out the footer you need to check for square even though the house may not be. Looking from the back yard on right façade go back 4 or 6 feet and set a string line. Now with string in hand secured to old wall walk to left past 5' footer location. Get a helper to look at line and bring it close to the wall and just seeing light between old brick wall and line. This is called tailing out a wall. Drive in stake secure string to stake. Now measure 5' from that old brick corner and mark the 5' Now toy should have two stakes set. One is the front finish on the 5' faced and one is where the return wall to house alcove. To check things for square I'm going to teach you Pythagorean theorem. The magic numbers are 3, 4, 5. 6, 8. 10, To square anything use these numbers in either the first 3 groups or the second three groups. So lets say on a corner you can measure 3in one way 4in opposite way right angle. From there to the previous 3inch mark should be 5 inch across which is a perfect 45 degree angle. Use the 6 8 10 the same way. The beauty here is the addition is 5'x10' so lest use the 3 4 5 so now it 3 feet down inside wall mark that and you have the 5 pin from those two marks point to point should be 5 feet. A perfect 45 which mean a perfect 90 on the corner.
I would get a good Mason to lay the block and brick. Of all the trades masonry is almost never a DYI project, The foundation below HAS to be dead on. When you dig the footer leave extra room on the front of the footer so the Manson can stand in ditch to lay block, So 24" wide footer. 10" block can sit 4 to 6" "in from edge of footer. So out of 24" wide, 14" of footer is used up. This leaves the Manson 18 to 20" left to stand in the ditch and lay block.
Makes you kind of wish I was there to build it. Your not alone I'm new to this site and I'm been VERY impressed with the other tradesmen here. And at times I think boy could all of us build a top notch structure together Im 34 years in the field and Im not impressed easily.
To find a good Mason I just thought of a good way. Ask him does he know 3, 4, 5, or 6, 8, 10, If those numbers means nothing to him than I would NOT consider him a Full Mason. Or ask him of he know Pythagagoras and his theorem? I learned this in 1974 at a high school Vo tec learning to be a mason. I posted site on him. I never looked it until now, just knew his name and theorem.
Pythagorean theorem - Wikipedia, the free encyclopedia
Sorry I got carried away, but here is a good trade secret and soon to be lost. Only a few on the site would know this. And who does, its defiantly a good sign of a true builder.
Signed 21 Boat
If I Helped To Answer Your Question Please Rate My Answer
|
|
 |
Full Member
|
|
Mar 11, 2009, 05:46 AM
|
|
So, thinking this over, what do you think of doing a slab with a turned down footing with a monolithic pour? Is that possible in this application?
|
|
 |
Ultra Member
|
|
Mar 11, 2009, 07:45 AM
|
|
No not for 3 stories. On top. You should have a 2' wide footer. Specks may say 18" wide. The problem here is being able to hold the outside form and the ditch below is two wide to center the pour wall part. So think of an 8" or 6" wide wall. The 6" block wall for the plate may be changed to an 8" block wall and then the block on footer then would change to 12" as opposed to 10" The code officer will let you know. Or the architect. For all of the forming problems here for as little as a block run you have stay with block wall to bring it out if the ground.
For as often As I put up a foundation I rarely go all pour. I only do it for a frost footer for a patio here. frost is 18" here.
Signed 21 Boat
If I Helped To Answer Your Question Please Rate My Answer
|
|
 |
Full Member
|
|
Mar 11, 2009, 07:47 AM
|
|
I guess I am just looking at having to have 2 separate, very small loads of ready mix delivered and was wondering if there is a way to avoid that?
|
|
 |
Ultra Member
|
|
Mar 12, 2009, 04:42 PM
|
|
Sure mix the footer by hand and deliver the floor load. The footer is about a half a yd. Get some Portland cement concrete sand and 2B clean stone delivered. I always mix it ourselves under a yd or so. The deliver here is over $100.00, plus sur charges etc. Environmental etc.
Signed 21 Boat
If I Helped To Answer Your Question Please Rate My Answer
|
|
 |
Full Member
|
|
Mar 12, 2009, 07:03 PM
|
|
Makes sense.
So I met the other day with a mason in the area and discussed the project with him. I just got his quote back. Can you let me know what you think?
The scope of work includes:
1) Footer
2) Foundation
3) Brick veneer (using brick salvaged from demo on the home)
4) New slab (demo the old and poor a new)
5) Convert one window in brick wall into a doorway
6) Cut new doorway in brick wall
The price is $4,600.
I know that prices differ from area to area and of course I plan on getting additional quotes, but does this seem reasonable? High? I have heard good things about the company and they are actually located just 2 blocks away from my home. He suggested doing things exactly as you have suggested.
Thanks!
|
|
 |
Ultra Member
|
|
Mar 12, 2009, 07:17 PM
|
|
That's a ***** of a good price. Even though it 5x10 it takes more time per output than a bigger Job. I call it Job rhythm. Break the rhythm and keep changing gears cost burn time
Get two more prices and the average will appear. Don't just look at price. A good tradesmen is always Worth it.
Signed 21 Boat
If I Helped To Answer Your Question Please Rate My Answer
|
|
Question Tools |
Search this Question |
|
|
Add your answer here.
Check out some similar questions!
Insulation of flat roof
[ 7 Answers ]
I just had the roof and plywood replaced over a 1950s addition. I exposed the rafters in the ceiling below. My question is, after I insulate with 6 1/2 kraft faced, what can I use for a vapor barrier, between insulation and sheetrock?
Tarping a flat roof
[ 2 Answers ]
Hello need some help trying to tarp a flat roof with a/c unit on it what is the best was to stop water from coming in around the units don't want to cover the a/c unit they will burn up
Attach gable roof to flat roof
[ 1 Answers ]
We are building a three season attached screenroom. We are uncertain how to attach the gable roof to the present roof (gabled in the opposite direction, so the attachment is on the flat side). We have spent hours trying to locate do it yourself instructions and can only find do it yourself kits...
Shingles not flat on new roof
[ 5 Answers ]
Just had a new roof installed with all new plywood etc. Looks like a fine job except that most of the shingles do not lie 100%flat on the bottom. Someone told me that it's because the weather is still cold (it was installed beginning of December in NY) and that if it were warm, that the shingles...
Roof framing
[ 1 Answers ]
How to lay out and cut roof rafters
View more questions
Search
|