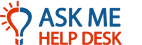 |
|
|
 |
New Member
|
|
Jan 31, 2009, 05:38 AM
|
|
Air compressor changing motor
I recently bought an air compressor with three phase power. I do not have three phase in this older property so I knew I would need to change the motor. I found a single phase 7.5 hp. Motor with the same shaft, etc. dimensions as the old three phase that I traded to a guy with the opposite problem.
He told me that it didn't have a mag starter so I ordered one. Now that I have the motor picked up I found that it is a capacitor start. So I guess no need for the starter.
Now the big question. So now I have a rebuilt motor on my compressor with none of the knock outs removed. I have a pressure switch with two wires in a casing hanging. I have a diagram that shows proper connection for direction so I am good there, and also on the ground placement.
How does this pressure switch wire into the motor ? I assume it runs inline with one of the power wires to cut it out at set pressure. Also, since a 3 phase motor came out of this with a magnetic start switch which has been removed and sent with the old motor I now have no switch for this new motor.
I have a service disconnect ( non-fused ) that will be within 5 feet of the compressor. Would this be my switch ? Or is there something I am really missing here. Do I need to get some type of actual switch for this motor which is a continuous duty, or is it wired direct with the service disconnect.
Basically I was good using the old configuration with the mag starter, but without the need for the starter I am now confused as to how the pressure switch wires in, and also if I need a switch.
Can anyone offer some suggestions ? Thanks !
|
|
 |
Outdoor Power Equipment Expert
|
|
Feb 1, 2009, 09:23 AM
|
|
Hi,
You have not said what model or brand this compressor is, but I think you have a bit of confusion as to the purpose of the switch versus the capacitor. The capacitor starts the motor with an extra burst of energy to get the rotation started. The magnetic switch turns the motor on and off based on the resistance to rotation that occurs as the pressure rises in the tank. The switch is still needed though it needs to be on to match the phase of the motor.
Peace,
Clarke
|
|
 |
New Member
|
|
Feb 1, 2009, 07:32 PM
|
|
Clarke, it is a Leroi Dresser compressor, but I am not sure of the model. The three phase motor was changed out due to no 3 phase service. Originally a 10 hp. 3 phase now a 7.5 hp. Single phase 230 v. with capacitors. The new motor is a farm duty same rpm, shaft size and length.
I believe that I have a problem with the wiring although I am not sure. The run from the main box is about 50 ft. I had this running yesterday but today it tried to start but then began to smoke. I shut it off within seconds and let it cool down. I then opened it up and the two hot leads coming from the pressure switch had melted. All of the wires in the motor look good. There was smoke coming from the capacitor area on top but I think it was also from the wires and just escaped through there as I do not see any burnt wires. I am hoping the motor has not been damaged.
The service is in a garage from an old panel. No breakers, just screw in fuses and two pulls with barrel fuses. Main is 2x60amps and the ( range ) compressor feed is 2 x 45 amps.
I was concerned about this but the feed going to the disconnect panel appears to be 12 gauge. Coming from the disconnect panel to the pressure switch is 10 gauge. But the two wires coming out of the switch to the motor are the original wires and are 12 gauge again.
The ground is 12 gauge to the disconnect and then 10 from there to the motor.
The ground was not damaged.
I pulled everything back out and it looks like only the two feeds from the pressure switch to the motor are melted. During the time the motor was trying to start it never did reach full speed before it smoked the wires and I shut it down.
All of the wiring is copper. It was previously used with a tig welder with no issues.
I found that I also have a problem in the main panel. The main disconnect had cracked and the previous owner had a piece of pvc pipe holding it in place. When I pulled the disconnect to check out the fuses it all fell apart. I put it back together and finally got things positioned where I have power to lights and receptacles. I have the feed to the compressor pulled, and also the disconnect panel is off. I think I may need to upgrade the main panel as well as the gauge of the feed and ground wiring to the disconnect to the compressor before I think about trying to run it again.
So, I have a 50 ft. run to the disconnect. Would it be safe to think I should use 8-2 wire ?
Should this be copper or aluminum ? From the disconnect box into the pressure switch and to the motor, could I then use 10-2 copper ? I may have a problem getting 8 to connect. Also, should I be using a magnetic switch with a capacitor start motor ?
I have heard some say yes and others say no. I want to make sure I am doing this correctly. If I need a mag starter then I will install one. If not let me know what I should be using.
As far as running new 8 gauge that is not a problem. With the service panel I can completely power down the garage and install a new panel. I can get the connections made and I have someone I can have come and look at it before it is powered up.
I have done some basics before, but 230 volts is somewhat new to me. I am really hoping the motor is still OK. It shut down because I shut it down. It didn't shut itself down.
I do have three meters. A MAC and two flukes. Is there a way to check the motor now that I have the wiring exposed to see if things are OK ? Like I said the motor wires all look Ok. They are not at all melted and neither are the capacitor wires. Only the two feed wires from the pressure switch melted.
Thank you
|
|
 |
Uber Member
|
|
Feb 1, 2009, 08:01 PM
|
|
Yo guys. The pressure switch very likely is not capable of handling the motor directly. Here is a simple pressure switch.
http://www.dwyer-inst.com.au/htdocs/...ure/CX_cat.pdf
Using a rudimentrary calculation of 746*7.5/240, I get 23 amps. Start current will be much higher.
The above pressure switch is only rated for 12. Your switch has to be Horsepower rated. A three phase pressure switch would use less current. Something like 23/sqrt(3).
A single phase motor starter seems essential.
e.g SCE2S series at a minimum
http://web2.automationdirect.com/sta...fujimc9150.pdf
|
|
 |
Outdoor Power Equipment Expert
|
|
Feb 1, 2009, 09:57 PM
|
|
Hi,
Have to agree with the above synopsis of the switch problem. The wiring is also underrated at 12 ga. 10 ga would be a minimum, copper is called for as another gauge step is necessary with aluminum.
I looked in various places for the brand. My guess is that it a P-series. That company evidently broke into pieces with three different companies buying different parts. It made small compressors, large trailer to railroad-car sized compressors, refridgerant compressor and medical application compressors.
Peace,
Clarke
|
|
 |
New Member
|
|
Feb 2, 2009, 05:09 AM
|
|
Ok, below is what I ordered for it. I assumed that is what it needed, but I was told since it had capacitor start it wasn't needed. On the old motor one leg went through the switch. I was told to run both through this one which I did. I am going to get the proper switch as well as wire in the starter then.
So you think 10 / 2 is enough ? I do not need to go up to 8 / 2 from the main panel to the disconnect
And then run 10/2 from the disconnect to the motor ?
And what do you think on the motor. Is there a way to check it or does it sound like the wires took the damage ?
Thanks
THIS IS A BRAND NEW IN THE BOX SQUARE D MAGNETIC STARTER W/ OVERLOAD/HEATER.
THIS IS A 7.5 HP 1 PHASE 230 VOLT STARTER W/ A 40 AMP CONTACTOR . IT COMES IN A NEMA 1 SIZE ENCLOSURE AND COMES W/ 1 B-62 OVERLOAD/HEATER.
HP: 7.5
VOLTAGE: 208-240
AMPS: 40
PHASE: SINGLE
ENCLOSURE: NEMA SIZE 1
HEATER: B-62 (MESSAGE ME IF YOU REQUIRE A DIFFERENT SIZE)
THE LIST PRICE ON THIS STARTER IS AROUND $210.00 THE MODEL # IS 8911DPSG42V09
THE COIL VOLTAGE RANGE IS 220-240 VOLTS AND THE STARTER CAN BE USED FOR 5-7.5 HP APPLICATIONS.
|
|
 |
Uber Member
|
|
Feb 2, 2009, 05:15 AM
|
|
Wires probably took the damage.
Here is the catalog information:
http://ecatalog.squared.com/pubs/Mot...8910CT9301.pdf
I have no idea why someone would tell you you didn't need a starter. The starter really isn't a starter in the true sense of the word. There are part-winding starters and Y-Delta starters for instance.
You have a capacitor start motor.
The starter is a definite purpose contactor and overload protection. The thermal overloads are sized based on the FLA on the nameplate of the motor.
Do you have the info from the motor nameplate? 7.5 HP is mechanical. Voltage and phase is nominal.
Overload is sized from name plate and duty rating.
Overcurrent and conductor size is sized by the tables.
|
|
 |
New Member
|
|
Feb 2, 2009, 06:26 AM
|
|
Here is the info. From the nameplate :
Doerr
LR-13758
Thermally protected Man.
1740 RPM
Hz. 60
Frame L 215 T
Lo volts 230 ( No Hi volts )
32.0 amps
Ph. 1
Type TF
Ser. Fact 1.0
Gode G
Insul class B
Max amb. 40deg. Cel.
Mtr ref. R91530FF831
Hope this helps !
Larry
|
|
 |
Uber Member
|
|
Feb 2, 2009, 10:03 AM
|
|
Purrfect:
Using THHW (wet) would yield #10 and #10 ground. Other wire such as UF will be #6 with a #10 ground. This is for intermittant duty, 15 min. Continuous duty will push it toward #6 and #10 ground. This is at 50 feet.
Using fuses:
Instantaneous trip: 125 Amps
Dual Element time delay: 70 Amps
Circuit breaker:
Instantaneous trip: 370 Amps
Inverse-time trip 100 Amps
Overloads:
They are technicly not required because the motor is thermally protected with a manual reset switch. There is a reset switch on the motor, correct?
There is probably only one T.U. or thermal overload here so the suggested TU is a B45.0. See table 145: http://ecatalog.squared.com/catalog/.../17416151.html
Some motors have an internal thermal overload that needs to be wired to the contactor.
Wiring:
For the control circuit, it's not normally required to break both conductors. You can if you like. Usually one provides fused 240, say 0.5 amp or so for both legs for the control wiring. The control wiring can be 14 AWG.
An on/off switch in series with the coil leads to the contactor would provide a means to turn on and off the compressor. A disconnect usually is not operated under load and neither would a circuit breaker. The disconnect should be rated for 46 amps.
The contactor is designed to switch the horsepower load reliably and quickly with arc suppression.
You should break both legs in the starter/contactor that go to the motor.
|
|
 |
New Member
|
|
Feb 2, 2009, 12:55 PM
|
|
Here is where I am at today. Compressor is still sitting with no wiring connected. I went and bought some 6/2 wire as well as a new service panel The old one needed to be updated and there are only 4 other circuits in there. I also picked up breakers for this and also a nre pressure switch from a compressor shop.
I will install the new panel with power disconnected to the garage. Wire in my existing 4 circuits and then run the new 6/2 to the disconnect ( 60 amp. )
Then run from the disconnect to the new mag. Starter and then to the motor.
2 wires from the pressure switch to the coil in the starter, is this correct ?
Also, I am confused on the breakers. Would a tandem 40 amp breaker not be sufficient ?
I probably should not have asked the guy at Menards, but he thought 40 should be plenty, and they had a little chart thing there. Or do you mean the two together ? So like a tandem 50 being 100 per the both.
I am a little confused on this part still. The panel is a 100 amp. It is in an old garage on an old farm. The old panel was just not good at all. The circuit I had planned to use had a pull out disconnect with fuses for a range. The main has a piece broken out so you have to jam pvc conduit in there to keep pressure. If not I lose all of my lights, and if I give it a push the other way I get the lights but lose the receptacles. It needed to be replaced but I never knew of the problems with it until now.
The welder was pretty much plug in and go with no problems.
Please let me know on the breakers I should run this circuit on. This has me confused.
I appreciate it !
Thank you,
Larry
|
|
 |
Uber Member
|
|
Feb 2, 2009, 01:29 PM
|
|
Here is where I am at today. Compressor is still sitting with no wiring connected. I went and bought some 6/2 wire as well as a new service panel The old one needed to be updated and there are only 4 other circuits in there. I also picked up breakers for this and also a nre pressure switch from a compressor shop.
I will install the new panel with power disconnected to the garage. Wire in my existing 4 circuits and then run the new 6/2 to the disconnect ( 60 amp. )
If this is a sub-panel, you should feed it with 4 wires. Ground, line 1, line 2 and neutral. Why not make the sub-panel from a 100A feeder. Since I think this is a detached structure, a ground rod is needed. This feeder should be wire sized for 100A * 125%. You might have to change the trip curve on this breaker too. Not sure if you have underground conduit in place or running underground cable. Your probably gong to have a couple of 120 circuits as well or at least try to.
You may just want to feed the compressor from afar to the disconnect and run another sub-panel. Now this could change the wire size based on the number of wires and what they are carrying in the conduit.
I'm also not sure if your using conduit and how many wires are in the conduit and what are they carrying?
Neutral and ground should be separate in the sub-panel and usually a ground bar kit has to be ordered as well. The neutral ground bond screw is also removed.
Then run from the disconnect to the new mag. Starter and then to the motor.
This seems correct.
2 wires from the pressure switch to the coil in the starter, is this correct ?
These are control wires. I'd use #14 AWG and pick off 240 from the disconnect side. Run to a switch (23 mm) diameter rotary and then to the coil and back to the return side (disconnect side) of the contactor.
Only use the disconnect when servicing the equipment.
Also, I am confused on the breakers. Would a tandem 40 amp breaker not be sufficient ?
Nope. 40 A won't do it. When one speaks of a double pole breaker (breakers joined) and each labeled 40 A, it's a 40 A double pole breaker. Not 80 A.
I need the make and model of your panel and the make and model of the breaker purchased.
The size of the breaker depends on it's trip curve.
|
|
 |
Uber Member
|
|
Feb 2, 2009, 02:05 PM
|
|
To help you understand breakers, I've included this article:
http://www.acaltechnology.com/datash...itbreakers.pdf
Motor loads are just plain weird. Initially they act like a short circuit when first turned on. When the motor is running the current is not in phase with the voltage. When it is, the Power Factor (PF) is 1. Power for sine wave currents and voltages is P = V(I)I(t)Cos(theta)
The breaker is there to provide short circuit protection, not to protect the motor. If the motor has a full load amps of 32 Amps, then a 40 A instantaneous breaker would trip every time on start-up. Thus when dealing with motors, you have to modify the trip curve or use a larger instantaneous breaker. You don't know where on the AC cycle the motor is going to start. It can start at zero volts or start at 240/2*sqrt(2) instantaneous volts. That amount of voltage introduced to just the winding resistance will overwelm an instantaneous trip breaker.
|
|
 |
New Member
|
|
Feb 2, 2009, 03:04 PM
|
|
Ok, the panel I picked up is a Square D QO series. QO112M100C
84127 100 Amps 12 spaces. The current panel is very old and has issues. The main disconnect has a piece broken from its enclosure and is being held by a piece of plastic conduit.
I think it is time to fix all of that.
So I will have a 100 amp service panel with breakers. What amp breakers should I use for this compressor ? I can't put 375 amp breakers in it, I don't think I have ever seen any of those.
I have 2 legs of 115 - 117 volts coming in. I have a ground that has had a rod added and a cable run into the ground bar.
It also has a neutral. The panel I bought has the 100 amp main and also the ground bar and a bar on the other side for neutrals as well.
I had to stick with this size panel due to being limited for space. Old garage with old thinking left little space.
I am still very confused on the breaker requirements. Even if I ran the delay breaker at 100 amps that would equal my whole panel. Can I even do that ? The motor is 32 amps. I guess I am in an area of power now that I really don't understand. We have another compressor in a different building with a 4 horse and 12 amps of current draw. We have a 20 amp tandem breaker and it runs fine. Why a 375 amp breaker ? I am not understanding this at all.
Thanks !
|
|
 |
New Member
|
|
Feb 3, 2009, 05:51 AM
|
|
A lot of this is Greek to me. Is the panel I picked Ok for this use ?
I will get the breaker info on later, but I made sure they matched the panel and were the more expensive ones.
I thought about going with the cheaper panel but then decided to get the more expensive.
I can disconnect all of the power coming into this as we have a few disconnect panels on a pole outside. Like I said, an old farm. All of the wiring here is overhead. I don't really like overhead, but old farm, and I can't afford to change all of it at this point.
With installing this 100 amp panel I will have 4 20 amp circuits for lights and receptacles. IDK but that is how they had it wired in and I figured it may be better to stick with what is working.
Then I will have the one for the compressor. I am just really confused at this point. The amps for the breaker is just baffling. I look at the charts you have provided and I can't figure them out so it is still hard to understand. I have been going on past experiences and comparables. I want to do this right and will wire from the motor backward, but this whole circuit breaker amperage thing has me just totally lost.
So I have a 50 ft. run with 6/3 wire and a ground. 7 1/2 hp. Single phase motor, capacitor start, adding a mag switch and new pressure switch, disconnect rated for 60 amps. Will run 14 gauge between the pressure switch and the coil in the starter.
Does this sound right ? Am I missing anything ?
Now to get straight with the breakers in the main panel to run this.
Larry
|
|
 |
Uber Member
|
|
Feb 3, 2009, 08:48 AM
|
|
Larry:
What you have in mind fr the pressure switch wiring makes sense. You'll have to make sure the pressure switch isn't fried.
You mentioned that you have a 4 HP/12 A on a 20 amp breaker. This is about 2x the rated current. The 7.5 HP/32A motor if using a 2x type idea then a 60 A breaker might work. The 50' will definitely lower the max current of the motor. You should be OK with a 40 A breaker. I misread the program I was using.
I looked over the load center and it appears it's basically for residential. There seemed to be a few different kinds of breakers available and I didn't have time to evaluate what I read. It also appeared that there is a 70A max for breakers in that 125A panel.
The total of breakers DO NOT have to add up to the main breaker amps. What does have to be respected is the maximum number of poles. This problem occurs because of some of the slim breakers which fit in a single space, but are for two independent circuits. Not sure if this panel accepts these. The breakers can have different ratings like 15/15, 15/20 or 20/20.
So far, so good.
a 7.5 HP motor is a BIG motor. How often do you expect it to run in a typical day or hour? Out of curiosity, what is it going to operate?
|
|
 |
New Member
|
|
Feb 3, 2009, 09:25 AM
|
|
Well, I picked up a new pressure switch yesterday. The last one was fried by running all of the voltage through it because I misread, or misinterpreted something.
It is a square D H.D. pressure switch. DO you think this would work with tandem 50 amp breakers ? I will run the 6/2 all the way to the disconnect, then to the starter and from the starter to the motor.
The 14 gauge will be from the pressure switch to the coil in the starter.
This probably will not run all that much when it is done. It will see much use in October and early September. The compressor is to supply air to pneumatic props in a Haunted attraction we put on every year. We have the 60 gallon in the Barn that ran everything last year, but ran out of air a few times so it was too much of a load on it. I need to look over that compressor very good before we start it up again. This new one will handle all of the props that require more air. The other ( smaller ) one will handle the smaller air props. Aside from that it will be used for some light air tool use and some paint spraying and sandblasting. When not in use for longer periods it will generally be shut down but run once a week to keep it in service and drain any water or moisture. You had me pretty freaked out with the 370 amp breaker. I was thrown by that one.
I build all of the pneumatic props in my garage and this year I am building some very large props. I am good with levers and building with wood and steel, but electricity sometimes confuses me. I was zapped by 277 volts some years back while working in a K-Mart store. I had shut down the power to the ballasts I was replacing but there was another circuit for emergency lighting that had the insulation cut through from when the wires were pulled. I have a huge respect for electricity now and will not touch it if I am not comfortable. I was somewhat hesitant on this project, but I figure with some guidance from this site, and my respect for what I am working with I should be OK.
I never want to get too comfortable, just feel confident enough with one project at a time.
I really appreciate the help and suggestions. I am not an electrician at any level. But I can see that you and others are.
I feel pretty good that the motor was not damaged and the wires took the damage. I have looked things over several times and have drawn up some diagrams on how I will proceed. No power will be sent to this motor until I have checked and re checked things. I do not want to screw this up again. And I certainly do not want to get hurt doing this. If you want, you can check out our website: The Haunted Barn It doesn't show a lot of the props, but a few. We have air cannons, an electric chair scene, creature crate, air blasters, jumping props, and more coming.
Thanks again.
|
|
 |
Uber Member
|
|
Feb 3, 2009, 10:35 AM
|
|
Wow! I'll look at the pictures on a speedier link.
Then really, the load should have been used so #6 is the appropriate wire.
Check into auto drains for the compressor. They are usually places at low poins of the lines. I don't think that they are too expensive.
Driers are. Driers are important for good spray painting. Also some valves need oilers in the lines to make a good seal unless the valves are suitable for dry air.
|
|
 |
New Member
|
|
Feb 3, 2009, 11:11 AM
|
|
This compressor has a big drier built on to the back of the belt shroud. Two big lines going to it. Also a big drain setup at the bottom, and we have a bunch of inline filters with low spots that have drain valves. I also added a regulator to this already as well as an oiler. We have more regulators throughout as well as some attached directly to the props. Most of the props are controlled by an electronic device with sound and programmed action. Some are more simple and controlled manually or with a wireless activation device. One had an air horn attached and actually puts people vertical.
Thanks !
Larry
Larry
|
|
Question Tools |
Search this Question |
|
|
Add your answer here.
Check out some similar questions!
Air compressor motor
[ 5 Answers ]
I have a 230 volt 15 amp 60 hz 1 ph air compressor motor I want to wire. I am little confused when I open the switch there is 1 black, 1 white and one ground. I am to assume that the white is to be hot to be 230 volts. I'm running 14/3 through out my walls with a 20 amp dual pole breaker. So in...
A/c compressor motor
[ 3 Answers ]
My a/c compressor motor will not start when I turn on down the thermastat unless I go outside and manually spin it to get it started. It will run for about 15 minutes and then it will stop again. I have to turn the air off for about 30 minutes and then I can turn it on and manually start it again...
New compressor motor
[ 3 Answers ]
Tried to connect my air compressor up and the breaker will not stay on. Other ansers make me believe this is a short, however, the wiring had no problems before and the motor is new. The breaker is a 30 amp, the motor only needs a 25.
Compressor motor shuts off.
[ 1 Answers ]
The compressor motor stopped running,(I was told it was bad) so I replaced it. When I started the unit back up it ran for a few minutes, but when the compressor tried to kick in it shuts off. I tried it several times but whenever the compressor tries to kick in it keeps shutting off. They gave me a...
Compressor Fan Motor keeps shutting off
[ 1 Answers ]
With the AC on and running the temperature started to rise in the house. I put my hand next to the register. Air was blowing but was not cool air. I went outside and the compressor fan motor wasn't blowing. On another occasion the same thing happened and I went outside and the fan motor was making...
View more questions
Search
|