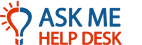 |
|
|
 |
New Member
|
|
Sep 19, 2007, 03:37 PM
|
|
Sub Panel Wiring
I'm running power to a new shop which is about 125 feet from the house. I would like to have 75 amp service at the shop. The service at my house is 200 amps and there is space in the panel for an additional breaker. I also have a separate 200 amp switch located next to the main panel that is used for switching the panel from standard service to a generator. This make it easy for me to connect to the mains if needed.
1. Would it be better to add 75amp breaker to the existing 200 amp panel and run this to the shop or add 75 amp panel (with breaker) from the mains? Obviously, the first choice is easier and cheaper.
2. Because of the cost of direct burial copper cable (6-3 with ground) what are my options with using aluminum? Is this available with insulation that can be buried or would this nesistate the use of PVC conduit?
3. Lastly, do I need to provide any additional grounding at the subpanel in the new addition?
Thanks.
|
|
 |
Junior Member
|
|
Sep 19, 2007, 07:57 PM
|
|
 Originally Posted by drs72
I'm running power to a new shop which is about 125 feet from the house. I would like to have 75 amp service at the shop. The service at my house is 200 amps and there is space in the panel for an additional breaker. I also have a separate 200 amp switch located next to the main panel that is used for switching the panel from standard service to a generator. This make it easy for me to connect to the mains if needed.
1. Would it be better to add an additional 75amp breaker to the existing 200 amp panel and run this to the shop or add an additional 75 amp panel (with breaker) from the mains? Obviously, the first choice is easier and cheaper.
2. Because of the cost of direct burial copper cable (6-3 with ground) what are my options with using aluminum? Is this available with insulation that can be buried or would this nesistate the use of PVC conduit?
3. Lastly, do I need to provide any additional grounding at the subpanel in the new addition?
Thanks.
I would recommend to always go with a conduit when something is buried into the ground.
Conduits aren't that expensive, and it's worth the money, if in the future you have
To rewire the shop for some reason.
Copper vs. Aluminum! Sounds like you are worried about the cost due to the length of
The cable you are going to use. I like copper over aluminum any time, but
If you have to spend a few hundred extra then I would probably chose Aluminum,
Even though I don't necessarily like to do that. So the question is, how much
More do you need to pay to go to copper, once you find the quote for Aluminum.
If it's under $100, then I would pay the extra if it was me.
Is your 75Amp breaker a 220v dual pole breaker?
|
|
 |
New Member
|
|
Sep 20, 2007, 03:43 AM
|
|
Thanks. Yes, I am running 240 VAC service and would be using a double pole breaker.
Are most wire types rated for underground conduit use? Since this would allow me to run single wires, it would help offset the cost (a little) of the conduit. Is underground conduit considered a dry location?
|
|
 |
Junior Member
|
|
Sep 20, 2007, 10:32 AM
|
|
Yes it is. Personally I would also go with conduit. And have a another panel for your shoup is a good idea. And not all wires are rated conduit use. Check your local store for specs
|
|
 |
Uber Member
|
|
Sep 20, 2007, 01:35 PM
|
|
Why 75 amp feeder? This is an odd size. If your using #6 for 75 amps because of the 90 Deg C column in the code, #6 can only be rated 75 amps if the terminals in the equipment at both ends are rated 90 Deg C, which you will not find. So you may use a 70 amp breaker.
My answers follow your questions.
1. Would it be better to add 75amp breaker to the existing 200 amp panel and run this to the shop or add 75 amp panel (with breaker) from the mains? Obviously, the first choice is easier and cheaper.
You have no choice but to install a breaker for the subpanel feeder into the main panel as a branch circuit. You cannot connect to the "mains"
2. Because of the cost of direct burial copper cable (6-3 with ground) what are my options with using aluminum? Is this available with insulation that can be buried or would this nesistate the use of PVC conduit?
There is a 4 wire aluminum cable called URD, Underground Residential Distribution, which uses USE cable, rated for direct burial.
For a 70 amp feeder the aluminum equivalent to copper wire is #4.
Conduit will be helpful as a sleeve for easy replacement and extra protection esp under paved areas.
3. Lastly, do I need to provide any additional grounding at the subpanel in the new addition?
You must run 4 wire feeder with the equipment ground. At the subpanel, the neutral is to be insulated and isolated and not bonded to the metal can. A separate equipment ground bar needs to be added, bolted directly to the metal can using machine thread screws, and connect only all the bare and green equipment ground wires to this bar. Only white neutrals will connect to the neutral bar.
The only wires rated to be direct buried will be USE insulation. This can be URD cable, UF cable, and individual USE wires
Buried conduit is to be considered as a wet location, and only wires with wet location insulation can be installed in buried conduit. The popular ones are THWN and XHHW, note that any insulation wet location rated has a W in the code.
|
|
 |
New Member
|
|
Sep 20, 2007, 03:08 PM
|
|
 Originally Posted by drs72
I'm running power to a new shop which is about 125 feet from the house. I would like to have 75 amp service at the shop. The service at my house is 200 amps and there is space in the panel for an additional breaker. I also have a separate 200 amp switch located next to the main panel that is used for switching the panel from standard service to a generator. This make it easy for me to connect to the mains if needed.
1. Would it be better to add an additional 75amp breaker to the existing 200 amp panel and run this to the shop or add an additional 75 amp panel (with breaker) from the mains? Obviously, the first choice is easier and cheaper.
2. Because of the cost of direct burial copper cable (6-3 with ground) what are my options with using aluminum? Is this available with insulation that can be buried or would this nesistate the use of PVC conduit?
3. Lastly, do I need to provide any additional grounding at the subpanel in the new addition?
Thanks.
I should have said 70 amps, my mistake.
I didn't mean to imply that I would run the mains all the way to the shop, but rather to a small panel consisting of only a single, 70 amp breaker and then on to the shop to another panel. I would suspect that this is what you'd do if your primary panel was filled. Fortunately, mine isn't, yet.
|
|
 |
Uber Member
|
|
Sep 20, 2007, 06:05 PM
|
|
OK Just where or how will the 2 circuit 70 amp panel/breaker get fed? Otherwise your plan sound fine.
|
|
 |
New Member
|
|
Sep 20, 2007, 08:26 PM
|
|
The service comes in through a 200 amp manual transfer switch. This allows me to switch from normal service to generator. This box is adjacent to the primary panel which is directly to the left of the transfer switch. I would add this small 70 amp panel at the right side of the transfer switch. The mains would be routed from here. I guess the real question is whether you can have 2 different panels coming from the same service entrance (mains). I may not be using the correct terminology and for which I apologize.
The logical answer (to me) is that, together, they cannot exceed the ratings of the main meter base. After thinking about this some more, adding a 70 amp breaker to the primary panel is probably the way to go. I am one to not try and push anything to it's limits, even though the primary is probably only at half its actual capacity.
I think I am going to use conduit for the wires to the shop. I have never pulled large wires, through conduit, this distance. Should I just plan on doing it in sections as I go? This is completely out of my experience level.
Thanks for your help.
|
|
 |
Junior Member
|
|
Sep 20, 2007, 09:53 PM
|
|
I am new to conduit installation as well. I went and bought PVC conduit 3/4 inch
For a single 14/2 romex wire, which was about 30 feet long, in mostly L-shape installation
For attic installation (kind of overkill, since conduit wasn't even required there).
A 3/4 inch conduit was certainly over sized for the wire I was using, perhaps
A 1/2 inch conduit was sufficient. However, I thought I buy a over size to make
The wire go through the conduit easier. I was surprised to find out that, the 3/4 inch elbows,
90 degree bends are narrower than the straight 3/4 inch PVC. Also, I was surprised
To have tough time pushing the 14/2 wire past the elbows. Later I found out that,
I needed to use a electrical fishing wire, and therefor pull rather than push
The cable through the conduit; even that is not that easy.
I would say, those heavy wires that you are going to pass through the conduit
For over 100 feet, definitely needs to be done right to make it easier on you.
I hope it is a straight run. Do you have to have elbows any where along the
Conduit?
Question is, if you do it in sections (which is something I tried as well), how
Would you cement the PVC conduit together while the wire is in the conduit,
Without getting the cement on the wire, and perhaps damaging the precious
And expensive wire, which can be hazardous too?
|
|
 |
New Member
|
|
Sep 21, 2007, 07:17 AM
|
|
I am fortunate in that it will be a straight run. As for gluing it, I doubt that a little adhesive will hurt the wire insulation, but I will test it first.
There's just no easy way to do this. If it was inside, I'd add some boxes ever few sections and pull through there, but that's the last thing I want buried. I have a fish tape, but not one of those Chinese finger webs to put over the wire to pull with. Might have to invest in one.
If anyone has some suggestions on pulling wire, this distance, through conduit, I'd certainly appreciate it.
|
|
 |
Uber Member
|
|
Sep 21, 2007, 11:04 AM
|
|
A conduit system is to be installed entirely , and then pull the wiring through.
This is where electricians earn their pay, wire pulling.
I guarantee you will have problems trying to lay the conduit and pull wire at the same time.
Do not allow PVC glue to get on the wire insulation. It will break down after time.
You can use a vacuum to suck or blow a nylon string through, use a plastic bag from a loaf of bread as a mouse as a leader on the string. Once the string is through, attached a 1/4" or larger rope, pull that thru , and use the rope to pull the wire.
If you strip about 6 in of wire and cut off most of the strands, leaving two or three on each wire, loop these and attach to the rope.
Tape the "head" well with tapered layers of electrical tape.
There is also wire lube available, do not use household soap.
A 70 amp feeder using #6 THWN wire will fit in a 1" PVC, for this long run I suggest 1-1/4" PVC conduit.
|
|
 |
New Member
|
|
Sep 21, 2007, 11:07 PM
|
|
 Originally Posted by drs72
I am fortunate in that it will be a straight run. As for gluing it, I doubt that a little adhesive will hurt the wire insulation, but I will test it first.
There's just no easy way to do this. If it was inside, I'd add some boxes ever few sections and pull through there, but that's the last thing I want buried. I have a fish tape, but not one of those Chinese finger webs to put over the wire to pull with. Might have to invest in one.
If anyone has some suggestions on pulling wire, this distance, through conduit, I'd certainly appreciate it.
Wire lube and a couple of good friends, one to help you pull, and one to feed the wires into the conduit. And beer for after, because you want them to still be your friends.
|
|
 |
Junior Member
|
|
Sep 24, 2007, 09:04 AM
|
|
 Originally Posted by tkrussell
A conduit system is to be installed entirely , and then pull the wiring thru.
....
Do not allow PVC glue to get on the wire insulation. It will break down after time.
Question:
1.How long does one need to wait pulling wire through PVC sch.-40 conduit, when it
Was just glued together ?
2.Would the glue be naturalized in seconds after it is applied?
3.How many #2 wires can fit inside 2" PVC ?
4.How many #2/0 wire can fit inside 2" PVC?
5.Is there a table we can use to figure this out, or is it more like a guess work,
And trial and error?
6.What are the wire sizes sold at home centers, i.e. is it the popular sizes,
Or is it the sizes manufacturers make? I see sizes, romex #14, #12, #10, #8,
#6, and for individual wires, THHN #4, #2, #2/0, #3/0, etc.
So where is #3, or #1, #1/0 ?
A note on the PVC conduit that I touched upon already in this article. When
I looked at the elbows, and other bends degree at the home center,
I have found the bends conduit connecting the straight conduits to
Be slightly narrower inside. It's kind of misleading. Wire, copper wire to be
Exact, is pretty firm. Pulling it through bends is much more difficult than a
Straight run. So one would want to increase the size of the conduit
To make that easier, but then we find that, just one size bigger, is
Not necessarily enough due to bends being actually smaller than the
Size of the straight conduit. How do experts solve this?
|
|
 |
Uber Member
|
|
Sep 24, 2007, 01:04 PM
|
|
My answers follow your questions.
1.How long does one need to wait pulling wire through PVC sch.-40 conduit, when it was just glued together ?
Usually only a few minutes, read and follow the instructions on the label.
2.Would the glue be naturalized in seconds after it is applied?
Not seconds, probably will be cured in 5-10 minutes. If the conduit is stressed too quickly the joints will come apart.
3.How many #2 wires can fit inside 2" PVC ?
4.How many #2/0 wire can fit inside 2" PVC?
Need to know the insulation, but I will assume THHN/THWN as a standard:
10-#2 THHN/THHW
5- #2/0 THHN/THWN
5.Is there a table we can use to figure this out, or is it more like a guess work, and trial and error?
Nothing in electrical is left to guess work. Ever read the code?
See: https://www.askmehelpdesk.com/electr...ons-48863.html
Go to Annex C- Conduit and Tubing Fill Tables.
Note there are no instructions to use this chart, so keep your wits about you. You must first find the appropriate chart for the raceway you chose, then find the insulation type, from there it is easy.
6.What are the wire sizes sold at home centers, i.e. is it the popular sizes,
Or is it the sizes manufacturers make? I see sizes, romex #14, #12, #10, #8,
#6, and for individual wires, THHN #4, #2, #2/0, #3/0, etc.
So where is #3, or #1, #1/0 ?
The home centers will stock what materials will be for the typical, basic, and popular size services and residential wiring, such as 100, 200 amp. The other sizes you mention are for other circuits, feeders, etc, that are more used for commercial, etc.
A note on the PVC conduit that I touched upon already in this article. When
I looked at the elbows, and other bends degree at the home center,
I have found the bends conduit connecting the straight conduits to
Be slightly narrower inside. It's kind of misleading. Wire, copper wire to be
Exact, is pretty firm. Pulling it through bends is much more difficult than a
Straight run. So one would want to increase the size of the conduit
To make that easier, but then we find that, just one size bigger, is
Not necessarily enough due to bends being actually smaller than the
Size of the straight conduit. How do experts solve this?
As long as the conduit is sized properly to handle the wires being pulled through, we have no problem with this issue. The usable area is still the same as the conduit, just a bit deformed. Steel sweeps have the same deformity, with no problems.
Note that the code is minimums and maximums, with limitations for everything. Doing an installation that exceeds the code is widely performed and recommended. Once all the detail of a feeder, for example, is determined, a judgment is made based on all the factors.
Annex C only lists the max number of certain size wires/insulations can fit into a conduit based on the popular 40% fill rule. Length, quantity of current carrying conductors, etc all need to be considered, not just how many wires can be crammed into a conduit.
Considering one of the examples you asked about, 10-#2 THHN will fit in a 2" PVC. If I had a reason to actually pull 10-#2, I doubt I would be using 2" PVC, unless the run was short. Probably would be using 2.5 or 3 inch for any length over 50 feet.
Another thing to consider, esp with PVC. We almost never use PVC sweeps, esp for long runs containing service entrance conductors. Utility companies widely demand that steel sweeps be used for conduit runs that will contain there wires. The friction of the heavy wires inside the pipe cause the wires to burn, or melt, through the wall of the PVC sweep.
|
|
 |
Junior Member
|
|
Sep 24, 2007, 01:35 PM
|
|
 Originally Posted by tkrussell
My answers follow your questions.
....
Another thing to consider, esp with PVC. We almost never use PVC sweeps, esp for long runs containing service entrance conductors. Utility companies widely demand that steel sweeps be used for conduit runs that will contain there wires. The friction of the heavy wires inside the pipe cause the wires to burn, or melt, thru the wall of the PVC sweep.
Are you saying that, galvanized metal pipes do not have friction issue,
Or if there are friction between metal and plastic coating of the wire,
It is negiable?
|
|
 |
Uber Member
|
|
Sep 24, 2007, 03:52 PM
|
|
Of course there is friction, but the PVC cannot take the heat, that remains static as the wire is pulled over it. The wire does not get affected as the friction is less due to the properties of the insulation, and it is constantly moving spreading the heat.
The metal on the other hand is not affected by the heat created.
How are you doing with Article 220? Fun reading, huh? Riveting plot.
|
|
 |
New Member
|
|
Sep 24, 2007, 06:43 PM
|
|
I've decided to run #4 (THWN) through a 1 1/2" conduit.
1. Does the ground ground wire also have to be #4 or can it be smaller?
2. It was suggested that I don't run a ground wire from the primary panel but rather connect a grounding rod at the sub panel. Would this meet code and are there specifications on the length, diameter, etc, for this grounding rod?
|
|
 |
Junior Member
|
|
Sep 24, 2007, 06:52 PM
|
|
Honestly, I am not sure if I can retain all the NEC rules I am reading.
It is challenging to find the correct materials at the home centers
To do the job right and do it safe. There are so much options in
Materials out there, it's unbelievable.
So, let me ask this, if you were doing electrical work for your own house,
Would you use galvanized metal pipes and buy the compression fitting
For bends, or just buy the PVC sch-40 pipes since it's lighter product,
It's easier to cut, it's cheaper, etc.
And
|
|
 |
Uber Member
|
|
Sep 25, 2007, 01:14 AM
|
|
PVC Schedule 40 with all the fittings, for all the reasons you mention.
|
|
 |
New Member
|
|
Sep 25, 2007, 04:46 AM
|
|
TK, would you mind moving up a thread or 2 and taking a look at my question regarding the grounding of a sub-panel. After doing some more reading, I don't feel that I can eliminate the EGC as suggested to me, so my question is how big that conductor needs to be and should I still utilize a grounding rod?
The service to my sub-panel will be coming up in the middle of my slab to an interior wall. Can the grounding rod be installed next to the conduit IE protruding from the slab or does it need to be spaced away from the building? Now I'm back to the proper conductor size to connect to the rod. Thanks for all of your help.
|
|
Question Tools |
Search this Question |
|
|
Add your answer here.
Check out some similar questions!
Wiring to sub-panel.
[ 1 Answers ]
Will this work properly if when wiring a sub-panel for 240v can one of the 3 aluminum 4 gauge wires in the pvc underground pipe be used as the neutral wire if that wire is bare?
I intend to attach the ground bus at the sub-panel to a ground rod using 6 gauge bare copper wire.
Welder Wiring / % of Panel Capacity
[ 3 Answers ]
I recently purchased a Lincoln Precision TIG 375 welder(here) at a business liquidation auction. It came with huge pin type connectors (shudda been a hint). After I got it home and read the manual, I discovered it requires a 175 amp breaker when used to it's max capability. I have 200 amp service...
Main to Sub Panel Wiring
[ 3 Answers ]
I received an answer prior to wiring this up, but am a bit confused. I think I was told to keep the ground separate at the sub panel but am not sure. If so, I only need to pull 3 wires (2 hot legs and 1 neutral). I have attached my PDF for your review.
Thanks,
...
Sub panel wiring
[ 1 Answers ]
I have a 50 amp GFCI breaker in my subpanel box to be used by a hot tub. I noticed that the breaker has a post for the neutral wire load. Is it necessary to use this post or can my load neutral wire be connected to the neutral bus (same as breaker pigtail and supply neutral)?
Sub panel 40 amp wiring
[ 1 Answers ]
I have a 70 amp sub panel. I'm trying to figure out how to wire in a 40amp breaker in the sub from the panel in my house. I have two hot wires coming in to separate lugs, one neutral, but the breaker itself has one trip/reset lever yet has two screws on the bottom of the breaker;one on each side....
View more questions
Search
|