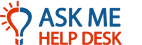 |
|
|
 |
Uber Member
|
|
Sep 16, 2007, 09:40 PM
|
|
42. Changing Spark Plugs
Remove old plugs when the engine is "stone" cold, to decrease the chance of stripping the aluminum head.
Use a 3/8-inch drive ratchet wrench, 6-inch quick-release extension bar (helps prevent socket from pulling off extension bar in the spark plug tube), and 5/8-inch spark plug socket. Spray the rubber insert in the spark plug socket with silicone spray, to further help prevent the socket from pulling off the extension bar in the spark plug tube. If you don't take these precautionary steps, the simple task of changing spark plugs can become frustrating. Otherwise, buy a GearWrench (#80546) magnetized extended 5/8" spark plug socket, with swivel. It eliminates the struggle of changing spark plugs. The magnetized core holds the spark plug in place and the extra long reach makes it easier to access tight spaces. It has a one-piece design, so the socket can't detach from the extension bar.
1. Remove the spark plug wire from the first plug. Carefully, remove the old spark plug. Check the gap of the new plug. I only recommend NGK spark plugs for Hondas--my experience with cross-referenced plugs has not been good. Normally, it's best to use the exact plug that came in the car. For hotter climates, use the next colder plug. Apply a thin coating of dielectric grease to the terminal nut and top porcelain insulator/corrugations of the new plug. Likewise, apply a half pea-size drop of anti-seize compound (preferably high-temperature nickel) to the lower threads, allowing rotation to spread the compound. If too much is used, plugs will "coke" in the holes. Insert spark plug in socket; attach extension bar; insert plug in hole; and tighten finger-tight, being careful not to cross-thread the plug. Some mechanics prefer to insert the plug into a 6-inch length of 3/8-inch I.D. neoprene hose, to prevent cross-threading the plug. Attach socket wrench and gently tighten the plug. Finally, use an inch-pound torque wrench to tighten the plug to the specified torque. Since anti-seize compound is a lubricant, reduce specified torque by 20% to prevent over-torquing and stripping threads.
2. Apply dielectric grease to the inside terminal of the spark plug wire, wipe wire down with silicone spray, reattach wire, and move on to the next plug.
3. Update Maintenance Log.
Change regular plugs every 24,000 miles or 24 months, whichever comes first. Change platinum plugs every 50,000 miles. Be careful not to leave platinum plugs in for more than 3 years or they may seize in the aluminum head. It's better to remove and reinstall them periodically.
|
|
 |
Uber Member
|
|
Sep 17, 2007, 09:41 AM
|
|
43. Changing Engine Oil and Filter
Always change engine oil, when the engine is hot. This allows a faster, more complete drain. If you change the oil when the engine is cold, dirt will cling to the sides of the block and pan.
1. Remove engine oil dip stick and filler cap, to facilitate draining and to prevent PCV valve contamination.
2. Place car on jack stands.
3. Place drain pan under car and remove oil filter, using a cap wrench and 3/8-inch ratchet wrench or a strap wrench.
4. Fill oil filter with engine oil, install filter, and torque to 16 ft.-lbs, using a cap wrench. Since most engine wear takes place at start up, filling the oil filter with oil prevents a "dry start." I recommend using premium oil filters. Premium oil filters have a red silicone rubber anti-drain back valve that makes a real difference in not allowing the oil to drain from horizontally-mounted oil filters overnight. This provides much quieter valves at startup. These new premium filters (e.g. PureOne, Amsoil Ea, and Mobil 1 EP) are worth the money, in my opinion. Filtration is rightfully the new "big thing" in lubrication.
5. Place drain pan under oil pan and, using a 17 mm box-end wrench, remove oil drain plug. When draining is complete, install drain plug hand-tight and torque to 33 ft.-lbs.
6. Lower car from jack stands.
7. Add recommend amount of approved weight engine oil to oil filler hole, using a funnel. I recommend buying the best full-synthetic lubricants available. I focus on European oil standards and buy engine oil that is both ACEA A3-rated and MB 229.3 or MB 229.5-rated for my vehicles. These are the toughest engine oil specifications in the world I'm aware of.
8. Replace oil dip stick and filler cap.
9. Start car and check for leaks. Ensure car is not overfilled with oil.
10. Update Maintenance Log--record "Date, Mileage, and Work Performed." Refer to it often. I use Microsoft Word and keep a Maintenance Log for each of my vehicles in my PC--it's incredibly handy and facilitates staying on top of maintenance.
11. Recycle old oil and filter.
Do your part to keep the air we breath clean, conserve oil and gasoline, and reduce global warming by using synthetic lubricants.
|
|
 |
Uber Member
|
|
Sep 20, 2007, 05:36 PM
|
|
45. Changing Power Steering Fluid
Only use Honda Genuine HG Power Steering Fluid, Part No. 08206-9002, or Amsoil's Synthetic Universal Power Steering Fluid (PSF). They must be Honda-specific. Using other fluids, such as ATF or other manufacturer's standard power steering fluid, will damage the system.
System Capacity: 1.1 liter (1.16 qt.)
Reservoir Capacity: 0.4 liter (0.42 qt.)
1. Raise reservoir and disconnect hose going to oil cooler.
2. Connect a suitable diameter hose to disconnected hose going to oil cooler; place other end of hose in a large, plastic jug.
3. Start engine, let it idle, and turn steering wheel lock-to-lock several times, to purge all old fluid and crud. When fluid stops running out of hose, shut engine off and discard fluid.
4. Reinstall return hose on reservoir.
5. Fill reservoir to upper level line.
6. Start engine, let it idle, and turn steering wheel lock-to-lock several times, to bleed air from system.
7. Recheck fluid level and add, if necessary.
8. Update Maintenace Log.
9. Recycle old fluid.
I recommend changing power steering fluid every 60,000 miles, due to the high expense associated with replacing pump, gearbox and valve body unit. More heat is developed in power steering units than most people realize.
|
|
 |
Uber Member
|
|
Sep 20, 2007, 06:39 PM
|
|
46. Changing Manual Transmission Fluid
Check fluid level with engine OFF and car on level ground
1. Warm engine to normal operating temperature.
2. Remove oil filler plug, using a 17 mm box-end wrench.
3. Remove drain plug, using a 3/8-inch ratchet wrench, and drain oil into a suitable pan.
4. Reinstall drain plug (using a new aluminum crush washer) and torque to 4.0 kg-m (29 lb-ft).
5. Add 1.8 liter (1.9 qt) of manual synchromesh transmission fluid, such as Amsoil 5W-30 Synthetic Manual Synchromesh Transmission Fluid (MTF), using a long-neck, transmission funnel. Alternatives are to add tubing to an existing funnel or use a pump. The oil level must be up to the filler hole.
6. Reinstall oil filler plug (using a new aluminum crush washer) and torque to 4.5 kg-m (33 lb-ft).
7. Update Maintenance Log.
8. Recycle old fluid.
No longer use 10W-30 or 10W-40 engine oil as manual transmission oil. Present engine oil formulations can damage the yellow metals in the synchros. Change every 30,000 miles or 24 months, whichever comes first
|
|
 |
Uber Member
|
|
Sep 27, 2007, 10:18 AM
|
|
19. Idler Pulley Bearing Replacement
Below is generic information for most modern-day vehicles:
Serpentine belt tension is set by the tensioner assembly, which consists of the spring tensioner and an idler pulley. Ideally, the tensioner assembly should be replaced when the serpentine belt is changed ($60.00+). In many cases, this is not the most cost-effective solution. Most people will replace the idler pulley, which costs about 30% of what the tensioner assembly costs ($18.00). For the more frugal, replacing the idler pulley bearing is an option ($1.80). Since space is normally tight on this side of the engine, access may be improved by moving the power steering reservoir aside or by removing the appropriate wheel and plastic wheel-well liner. Here's how to replace the bearing:
1. Remove idler pulley from tensioner, normally by using a 15 mm combination wrench.
2. Press out the old bearing. On many domestic cars, it's easy to drive the old bearing out of steel pulleys, using the ball end of a 32 oz. ballpein hammer on an anvil.
3. Place the new bearing in the freezer overnight. After heating the pulley with a hair dryer, the bearing should be easy to press in. Use a vise or shop press, if necessary.
4. Button things up.
The idler pulley should now be as good as new. Tighten the 15 mm mounting bolt 20 lb.-ft. on a standard NTN 6203 bearing, with a 17 mm inside diameter. This common bearing is frequently referred to as a "203" bearing.
|
|
 |
Uber Member
|
|
Oct 28, 2007, 06:35 PM
|
|
47. CV Driveshaft: Inspection
The following generic information applies to all FWD cars.
1. Driveshaft Boot. Check boots on each driveshaft for damage, cracks, leaking grease, or loose bands. Replace boots and bands, if damage is found. Try to do this at each oil change. Regular inspection may save a CV joint from replacement, allowing it to be repacked instead. Look for grease being flung all over the caliper, tire, and wheel. Don't be afraid to apply pressure to the boots and thoroughly examine them.
2. Twists or Cracks. Ensure driveshaft is not twisted or cracked. Even though this is unusual, it does happen. Replace driveshaft, if necessary.
3. Spline Looseness. Rotate driveshaft, by hand, and ensure spline and joint are not too loose. Replace inboard joint, if damage is discovered.
|
|
 |
Uber Member
|
|
Oct 28, 2007, 07:31 PM
|
|
CV Driveshaft: Removal
The following information is Honda specific.
1. Raise front of car and support on jack stands.
2. Remove lug nuts and front wheels.
3. Drain transaxle fluid. Often, this is unnecessary.
4. Raise locking tab on spindle nut and remove nut. With an air impact wrench, just back it right off.
5. Remove damper fork nut, bolt, and damper pinch bolt. Replace damper pinch bolts, if you can easily thread a non-self-locking nut past their nylon locking inserts.
6. Remove damper fork.
7. Remove cotter pin from lower arm ball-joint castle nut and remove nut.
8. Install 12 mm hex nut on ball-joint. Ensure hex nut is flush with ball-joint's pin end; otherwise, the threaded section of ball-joint pin might be damaged by ball-joint remover.
9. Remove ball-joint, using a ball-joint remover, from lower arm. Ensure ball-joint boot is not damaged. Apply Kroil or PB Blaster, if necessary, to loosen ball-joint.
10. Pull knuckle outward and remove driveshafts's outboard joint from front wheel hub, by using a plastic mallot.
11. Pry driveshaft assembly, using a pry bar or large screwdriver, from transaxle. This will force the set ring, at the driveshaft's end, past the groove.
12. Pull inboard joint and remove driveshaft from transaxle. Be careful not to pull on the driveshaft, as the inboard joint may come apart. To avoid damaging the differential oil seal, use care prying the assembly out. Be sure to pull it straight.
If the CV joint clicks, it's pretty much a waste of time trying to repair the axle--instead, replace it. This is particularly true, since the price of axles has dropped so much.
|
|
 |
Uber Member
|
|
Oct 29, 2007, 09:06 AM
|
|
CV Driveshaft: Disassembly
The following information is Honda specific. Honda does not recommend disassembling the outboard joint.
1. Clamp driveshaft in a vise with soft jaws.
2. Remove set ring from inboard joint.
3. Remove boot band, by prying up locking tabs with a screwdriver and raise end of band. If the boot band is the welded type, cut it off. Be careful not to damage the boot.
4. Mark each roller and inboard joint, to identify locations of rollers and grooves in the inboard joint.
5. Remove the inboard joint from the vise and place it on a shop towel on top of the workbench. Be careful not to drop the rollers, when separating them from the inboard joint. Examine splines for wear or other damage, check inside bore for wear, and look for any cracks.
6. Mark rollers and spider, to identify locations of rollers on spider.
7. Remove rollers and circlip (KD Tool 2534).
8. Mark spider and driveshaft, to identify position of spider on shaft.
9. Remove spider with a bearing puller.
10. Remove stopper ring.
11. Wrap driveshaft splines with vinyl tape, to prevent damage to boots and dynamic damper.
12. Remove boot band and inboard boot.
13. Remove dynamic damper band and dynamic damper.
14. Remove outboard boot bands, boot, and vinyl tape.
15. Inspect outboard joint for cracking, splitting, wear, and faulty movement. If any roughness or excess play is felt, replace the outboard joint.
16. Check outboard ring for damage.
If the boots are split, and need to be replaced, use a pair of diagonal cutters to cut the bands off; then, cut the boots off with a utility knife.
|
|
 |
Uber Member
|
|
Oct 29, 2007, 10:08 AM
|
|
CV Driveshaft: Repacking and Reassembly
The following information is Honda specific.
1. Wrap splines with vinyl tape, to prevent damage to boots and dynamic damper.
2. Install outboard boot, dynamic damper, and inboard boot to driveshaft. Remove vinyl tape.
3. Install stopper ring into driveshaft groove. Rotate stopper ring in its groove, to ensure it's fully seated.
4. Install spider on driveshaft, by aligning marks on spider and end of driveshaft.
5. Fit circlip into driveshaft groove. Rotate circlip in its groove, to ensure it's fully seated.
6. Pack outboard joint with joint grease included in the new driveshaft set (90 to 100 gm or 3.2 to 3.5 oz.). Amounts may vary with vehicle. Use Honda CV Joint Grease Outboard (Black), Honda Part No. 08798-9007.
7. Fit rollers to spider, with high shoulders facing outward. Reinstall rollers in their original positions on spider, by aligning the marks. Hold driveshaft pointed up, to prevent spider and rollers from falling off.
8. Pack inboard joint and inboard boot with joint grease included in new driveshaft set (120 to 130 gm or 4.2 to 4.6 oz.). Amounts may vary with vehicle. Use Honda CV Joint Grease Inboard (Yellow), Honda Part No. 08798-9003.
9. Fit inboard joint onto driveshaft. Reinstall inboard joint onto driveshaft, by aligning marks on inboard joint and rollers. Hold driveshaft assembly pointed up, to prevent inboard joint from falling off.
10. Adjust length of driveshafts to specs, then adjust boots to halfway between full compression and full extension. The ends of boots seat in groove of driveshaft and joint.
11. Install new boot bands on boots and bend both sets of locking tabs.
12. Lightly tap on doubled-over tab portions, to reduce height.
13. Position dynamic damper as shown below. Install new dynamic damper band and bend down both sets of locking tabs. Lightly tap on doubled-over tab portions, to reduce height.
Left: 75 +/- 2 mm (3.0 +/- .1 in.)
Right: 55 +/- 2 mm (2.2 +/- .1 in.)
Note: These representative figures may vary, depending on the car. Therefore, check the specs for your vehicle.
14. Install new set ring onto driveshaft or intermediate shaft groove.
|
|
 |
Uber Member
|
|
Oct 29, 2007, 10:36 AM
|
|
CV Driveshaft: Installation
The following information is Honda specific.
1. Install outboard joint in knuckle; then, loosely install a new spindle nut.
2. Insert inboard end of driveshaft into differential, until set ring locks in groove. Ensure inboard joint bottoms into differential and that set ring locks into groove of side gear.
3. Install damper fork over driveshaft and onto lower arm. Install damper in damper fork, so aligning tab is aligned with the slot in damper fork.
4. Loosely install damper pinch bolt, and a new damper fork nut with the bolt. The bolts and nut should be tightened with vehicle's weight on the damper. See Step 8, below.
5. Install knuckle on lower arm. Tighten castle nut (50 to 60 N-m or 36 to 43 lb-ft) and install a new cotter pin. Torque the castle nut to the lower torque specification; then, tighten it only far enough to align slot with pin hole. Do not align nut by loosening.
6. Tighten the new spindle nut.
7. Install front wheels (110 N-m or 80 lb-ft).
8. Tighten damper pinch bolt and new damper fork nut. Tighten damper pinch bolt to 44 N-m or 32 lb-ft. Tighten damper fork nut to 65 N-m or 47 lb-ft.
9. Refill transaxle, if necessary, with recommended fluid.
10. Check front wheel alighment and adjust, if necessary.
|
|
 |
Uber Member
|
|
Jan 10, 2008, 02:08 PM
|
|
52. PCV Valve Replacement
Perform every 60,000 miles or 4 years, whichever comes first.
1. Disconnect PCV Valve hose from throttle body, using a pair of pliers to remove spring clamp.
2. Remove PCV Valve and hose from intake manifold.
3. Disconnect PCV Valve from hose, using a pair of pliers to remove the other spring clamp. Using a spray can of brake cleaner, with the "straw" attached, spray inside of hose. This will remove any residual sludge, dirt, and sand. Take a pipe cleaner, dipped in fuel injector cleaner, and clean the port on the throttle body.
4. Install cleaned hose to a new PCV Valve and button everything up.
This will help your engine idle and perform better, last longer, and reduce emissions. Synthetic oils, with their lower NOACK Volatility (evaporation due to heat) characteristics, greatly reduce PCV Valve and hose contamination.
|
|
 |
Uber Member
|
|
Jan 25, 2008, 10:21 AM
|
|
6. Preventing Coil-On-Plug (COP) Problems
Many repair shops are reporting a large number of coil-on-plug (COP) failures with engines. The majority of problems are related to 1) customers washing their engines, or 2) body repair shops hosing off engines after repairing hood hail damage. Water seeps into the spark plug hole, where engine heat converts it to steam, and damages the coil.
Here are some rules to prevent the problem:
1. Never wash the engine, unless you cover the coils.
2. Always replace spark plug boots, when you change plugs.
3. Always replace the spark plug, when you replace a coil.
4. Always apply silicone dielectric grease to the rubber seal on the coil, where it connects to the engine; e.g. Motorcraft Silicone Brake Caliper Grease and Dielectric Compound (XG-3-A).
|
|
 |
Uber Member
|
|
Jun 21, 2008, 12:01 PM
|
|
24. Fuel Injector Replacement
1. Depressurize fuel system. On many Hondas, it's as simple as removing the gas cap. Other cars require removing the connector to the inertia switch in the trunk, or pulling the under-hood fuse to the fuel pump, starting the car, and waiting for the engine to stumble.
2. Disconnect negative battery cable.
3. Remove connectors from injectors.
4. Disconnect vacuum hose and fuel return hose from fuel pressure regulator. Place a rag over hoses, before disconnecting.
5. Disconnect fuel hose from fuel rail.
6. Loosen retainer nuts on fuel rail and harness holder.
7. Disconnect fuel rail.
8. Remove injectors from intake manifold.
9. Slide new cushion rings onto fuel injectors.
10. Coat new O-rings with clean engine oil and place on injectors.
11. Insert fuel injectors into fuel rail first.
12. Coat new seal rings with clean engine oil and press into intake manifold.
13. Install fuel injectors and fuel rail assembly into manifold. NOTE: To prevent damaging O-rings, install fuel injectors in fuel rail first, then install them in the intake manifold.
14. Align center line on connector with mark on fuel rail, if applicable.
15. Install and tighten retainer nuts.
16. Connect fuel hose to fuel rail with new washers.
17. Connect vacuum hose and fuel return hose to fuel pressure regulator.
18. Install connectors on injectors.
19. Turn ignition switch to ON, but do not operate the starter. After fuel pump runs for approximately two seconds, the fuel pressure in the fuel line rises. Repeat this two to three times, then check for fuel leaks.
|
|
 |
Uber Member
|
|
Jul 12, 2008, 07:55 PM
|
|
21. Reading a Tire's Manufacturing Date
Studies show that tires more than 6 years old can be very dangerous. Ensure that your "new" tires were recently manufactured, not sitting in the warehouse for years. Here's how to read the code on tires; for example, (3307) means the tire was manufactured in the 33rd week of 2007. The tire's manufacturing date is imbeded in the last code on the tire.
|
|
 |
Uber Member
|
|
Aug 11, 2008, 08:02 AM
|
|
13. Eliminating Air Conditioning System Odors
Air conditioner odors can be unpleasant and unhealthy. Here's an inexpensive approach to get rid of the problem. Mix a solution of liquid dish soap and bleach in a spray bottle. Attach a suitable hose and pump the solution in the evaporator coil drain tube, which is located on the passenger's side of the firewall. Be sure to insert the hose all the way in. Afterwards, flush everything out with clean water.
|
|
 |
Uber Member
|
|
Aug 29, 2008, 09:56 PM
|
|
Work in Progress.
|
|
 |
Uber Member
|
|
Nov 7, 2008, 09:40 AM
|
|
14. Importance of Changing Automatic Transmission Filter
The link below highlights the importance of dropping and cleaning the transmission pan, changing the transmission filter (each time), and refilling with automatic transmission fluid every 30,000 miles:
http://www.amsoil.com/lit/filter_man_council01.pdf
|
|
 |
Uber Member
|
|
Nov 9, 2008, 03:03 PM
|
|
8. Antifreeze: Automaker Approved Chemistry
Using the wrong antifreeze in your vehicle can be a costly mistake. No "one size fits all" antifreeze is approved for use in all vehicles. Play it safe and consult your Owner's Manual. The link below may help:
http://www.valvoline.com/pdf/Zerex_CoolantChart.pdf
Use a 50/50 mixture of approved antifreeze and distilled water, in order to minimize deposit buildup (cheaper and better). Otherwise, buy prediluted ready-to-use coolant, which is a 50/50 mixture of antifreeze and demineralized water (more expensive, but convenient).
|
|
 |
Uber Member
|
|
Nov 16, 2008, 06:37 AM
|
|
5. How-to Clean the Mass Air Flow (MAF) Sensor
Cleaning the MAF Sensor can increase gas mileage, horsepower, and general performance. This sensor measures air velocity, which the computer uses to determine proper air/fuel mixture. When the sensor gets covered with oil, dust, pollen, and air filter fibers, it results in a "rich" running engine, loss of power and higher emissions. Many recommend cleaning this sensor every time the air filter is changed.
1. Disconnect negative battery cable.
2. Remove screws (usually two Security Torx T-20) securing MAF Sensor to air intake and carefully remove sensor.
3. Place sensor on a clean rag and spray hot-wires or hot plate with CRC MAF Sensor Cleaner 10 to 15 times, being careful not to touch the hot-wires. Be sure to spray all sides of the sensor and clean all wires and connectors. Other chemicals, such as brake cleaner and carburetor cleaner, are considered too aggressive, even though some people use them.
4. Allow sensor to thoroughly dry for 45 minutes.
5. Reinstall sensor in air intake and button everything up.
|
|
 |
Uber Member
|
|
Nov 23, 2008, 10:38 AM
|
|
6. How-to Change the Fuel Filter on Most Ford Cars and Trucks
The inline fuel filter is usually located under the car, just in front of the right rear wheel. On many Ford pickup trucks, it's located in front of the left rear wheel. Be sure to wear safety goggles and keep a fire extinguisher handy. Change fuel filter every 30,000 miles.
1. Raise vehicle and support securely on jack stands.
2. Depressurize the fuel system. The usual recommendation is to disconnect the inertia switch connector, usually located in the right-rear trunk trim panel, start the car, and allow the engine to stumble. Removing the connector cuts power to the fuel pump. I prefer the following TRICK: Pull the under hood fuel pump fuse (much easier). On my 2000 Ford Taurus, it's Fuse No. 16 (20A). Check your Owner's Manual. On many Ford pickup trucks, remove the fuel pump relay from the under hood fuse/relay box.
3. Clean fittings on each end of filter.
4. Disconnect hairpin clips from the filter, by carefully prying upward with a small screwdriver. Separate fuel line from connector nipples on both ends of the filter, using a large screwdriver. On pickup trucks, use a 5/16" angled fuel line disconnect tool (Lisle 39410). If the inside release mechanism (spring) is rusted, spray with WD-40, PB Blaster, or Kroil.
5. Remove filter from bracket and install new filter, noting the flow direction arrow. TRICK: Use plastic caps, that come with some filters, to prevent spilling gasoline from old filter. Retighten clamp.
6. Reattach fuel lines, making sure they are fully seated, and install new hairpin clips.
7. Reconnect inertia switch connector or replace fuel pump fuse/relay. It's good technique to clean oxidation from fuse or relay contacts (#240 abrasive cloth or steel wool) and lightly coat with dielectric grease.
8. Start engine and check for fuel leaks.
9. Update maintenance log.
|
|
Question Tools |
Search this Question |
|
|
Check out some similar questions!
How to troubleshoot, repair & Maintain 92 Accord
[ 1 Answers ]
I replaced my distributor on 92 accord following you instructions. However, towards the end, it says that I need to read section C and D to precisely set idle speed and ignition timing. Can you tell where I can find those Sections? Thanks.
View more questions
Search
|